Performance dell'acciaio: performance ambientale
Performance dell'acciaio: performance ambientale
Emissioni di CO2 e prevenzione dei cambiamenti climatici
Le emissioni di CO2 del settore
2020 emissioni dirette di CO2: -21% rispetto al 2019.
La produzione di acciaio è un’attività “energy intensive” e comporta inevitabilmente l’emissione in atmosfera di CO2, sia in forma diretta (scope 1) per esigenze di processo e di combustione nelle diverse fasi del ciclo produttivo, sia di tipo indiretto principalmente per il consumo di energia elettrica (scope 2).
- Nella produzione a ciclo integrale il principale contributo emissivo è dovuto al rilevante input di carbonio necessario al processo di riduzione del minerale di ferro in altoforno e alla produzione e utilizzo del coke.
- Nel ciclo a forno elettrico le emissioni dirette sono molto ridotte e attribuibili principalmente ad agenti riducenti e di processo facenti parte della carica, oltre alle emissioni di combustione del gas naturale per esigenze di riscaldo. La parte preponderante delle emissioni attribuibili al processo EAF sono di tipo indiretto, associate cioè al consumo di energia elettrica (qualora prodotta da fonte fossile) necessaria per fondere il rottame di acciaio.
- Le emissioni di CO2 delle attività di lavorazione e trasformazione dell’acciaio (laminazione a caldo, forgiatura, ecc.) sono invece essenzialmente dovuta alla combustione di gas naturale nei forni di riscaldo o trattamento termico.
Nel 2020 le emissioni dirette di CO2 della siderurgia italiana (impianti di produzione e trasformazione acciaio inclusi nel sistema ETS) sono state pari a circa 8,3 milioni di tonnellate1, con una riduzione del 21% rispetto al 2019.
Tale riduzione è proporzionalmente più accentuata rispetto al calo della produzione (-12%) anche per effetto della maggiore contrazione della produzione di acciaio da ciclo integrale (a maggiore intensità emissiva) rispetto a quella da forno elettrico.
Le emissioni dirette e indirette della siderurgia 2020 contano per il 4,5% delle emissioni nazionali complessive di gas serra.
Se consideriamo anche le emissioni di CO2 indirette (dovute al consumo di energia elettrica negli impianti siderurgici) e quelle associate alla combustione di gas siderurgici di processo per la produzione di energia elettrica e calore, si può stimare per il 2020 un valore complessivo di emissioni, direttamente o indirettamente attribuibili alla siderurgia pari a circa 17,5 milioni di tonnellate di CO2 nel 2020. Confrontando questi numeri con quelli riportati nell’ultimo inventario nazionale dei gas serra pubblicato da ISPRA, si può stimare che tali emissioni coprano circa il 4,5% delle emissioni nazionali complessive di gas serra.
L’andamento delle emissioni rispetto al 1990
I dati ufficiali pubblicati dall’UNFCCC evidenziano che le emissioni di CO2 della siderurgia italiana si sono più che dimezzate sia in termini assoluti che in termini specifici dal 1990 al 2019.
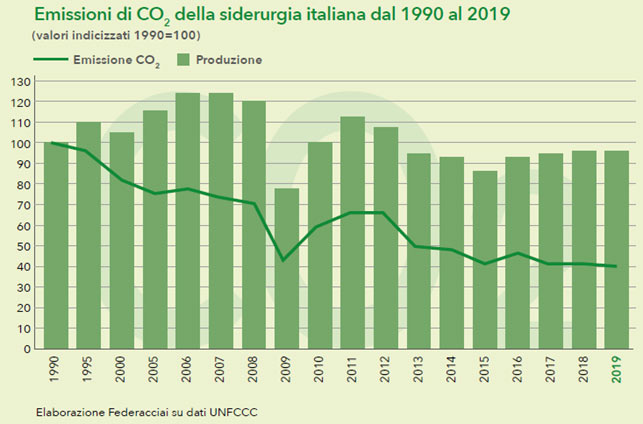
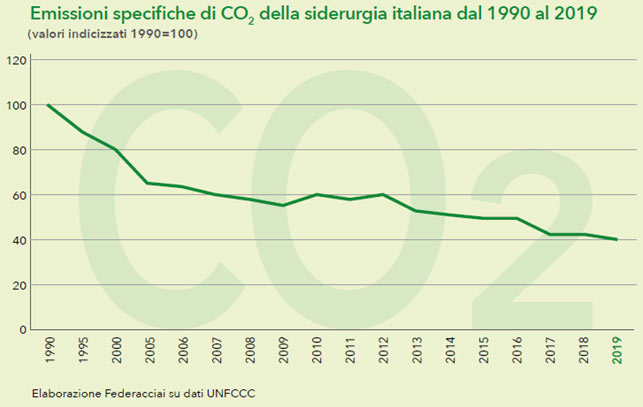
La riduzione di emissione di CO2 della siderurgia italiana -60% dal 1990 ha contribuito al raggiungimento degli obiettivi climatici dell’Italia al 2020.
Secondo i dati dell’ultimo inventario nazionale delle emissioni di gas serra pubblicato da ISPRA (Report 2021)5, e riferito al periodo 1990-2019, l’Italia avrebbe raggiunto una riduzione complessiva di circa il 22,7% delle emissioni di CO2.
Questi numeri evidenziano come la riduzione delle emissioni di CO2 nel settore energetico e industriale e di quello siderurgico in particolare siano stati determinanti per consentire all’Italia di centrare gli obiettivi climatici fissati al 2020, in linea con le politiche dell’Unione europea (c.d. strategia 20-20-20 al 2020).
Lo schema ETS
Uno degli strumenti fondamentali delle politiche climatiche dell’Unione europea è costituito dallo schema ETS (Direttiva 2003/87/CE), che a partire dal 2005 ha introdotto un sistema di tipo “cap and trade” di scambio delle quote di emissione. Il sistema attraverso la fissazione ex ante di un tetto annuale (cap) alle emissioni decrescente nel tempo, garantisce in maniera vincolante il raggiungimento dei target di riduzione complessivi all’interno del perimetro dei settori rientranti nel suo campo di applicazione (produzione di energia elettrica, principali settori manifatturieri energivori e in maniera differenziata, il trasporto aereo).
Per effetto dell’entrata in vigore della normativa Emission Trading (Direttiva 2003/87/CE e s.m.i.) le emissioni di CO2 degli impianti siderurgici sono rigorosamente monitorate dai gestori, calcolate applicando un rigoroso bilancio di massa tra il carbonio in ingresso e in uscita e verificate da un ente terzo indipendente, comunicate e registrate su un apposito registro pubblico europeo (EUTL- European Union Transaction Log).
Il 2020 costituisce l’ultimo anno del terzo periodo ETS (2013-2020) e lo spartiacque con la quarta fase ETS (2021 -2030), regolata da norme che sono state aggiornate e riviste ai sensi della Direttiva. È possibile quindi tirare le somme in merito all’andamento delle emissioni del comparto siderurgico nella terza fase ETS. Nel grafico seguente sono riportate le emissioni dal 2013 al 2020 di un campione costituito dalla maggior parte delle acciaierie italiane (il campione comprende impianti di produzione a ciclo integrale e a forno elettrico, inclusa l’attività di laminazione integrata nello stesso sito produttivo).
Rispetto a questo campione si evidenzia un calo dal 2013 al 2020 delle emissioni assolute del 29% e di quelle specifiche (t CO2/t acciaio) del 17%.
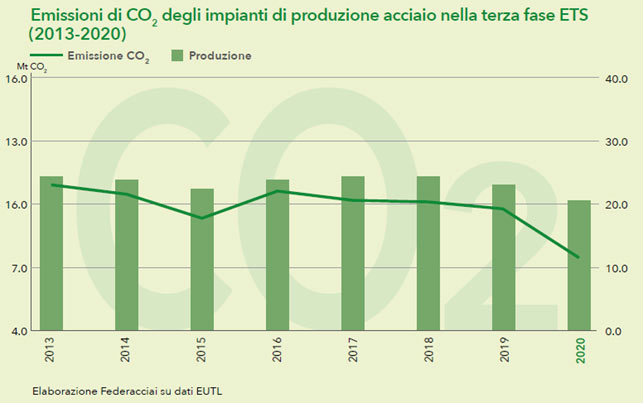
Gli obiettivi del Green Deal e il processo di decarbonizzazione verso la neutralità climatica al 2050
La lotta ai cambiamenti climatici costituisce indubbiamente il caposaldo principale del programma Green Deal lanciato dalla nuova Commissione UE a fine 2019. In attuazione di questo programma a giugno 2021 è stata definitivamente approvata dal Parlamento UE la Legge sul Clima, che innalza in maniera molto significativa il livello di ambizione europeo di riduzione delle emissioni per il medio e lungo termine. In particolare il target di riduzione UE al 2030 viene portato dal -40% fino al -55% (rispetto al 1990) e si introduce l’obiettivo vincolante di raggiungimento della neutralità climatica entro il 2050.
Questi nuovi obiettivi impongono una forte accelerazione già a partire dai prossimi anni dei processi di transizione energetica ed ecologica in tutti i settori dell’economia e della società, costituendo una sfida particolarmente complessa per l’industria manifatturiera energy intensive e in particolare per quei comparti fortemente esposti alla concorrenza internazionale come quello siderurgico.
Il percorso di decarbonizzazione pianificato dall’UE per i prossimi decenni comporta infatti una trasformazione radicale dei processi industriali sia nel settore della produzione/trasformazione di acciaio che in quello dei settori utilizzatori, nonché del modo di produrre e utilizzare l’energia, richiedendo investimenti ingenti in nuove tecnologie e infrastrutture. I vincoli imposti dal sistema ETS dell’UE, che sarà reso più stringente per adeguarlo ai nuovi obiettivi, e la conseguente necessità di acquisto dei permessi di emissione (il cui prezzo ha raggiunto già nel 2021 il massimo storico con un trend previsto in forte crescita nei prossimi anni) comporteranno contestualmente un forte aumento dei costi operativi per le imprese.
L’industria siderurgica nazionale riconosce l’importanza che l’UE mantenga un ruolo di leadership mondiale nella lotta ai cambiamenti climatici ed è pronta a fare la propria parte investendo risorse e competenze in questa sfida assolutamente ineludibile per le nuove generazioni, ma per raggiungere gli obiettivi condivisi è fondamentale creare le condizioni al contorno affinché il settore rimanga competitivo per tutta la fase di transizione e possa in questa modo mettere in campo gli investimenti necessari.
Si stima che l’UE contribuisca oggi per circa il 9% delle emissioni globali di CO2 e questa percentuale, in continua diminuzione, tenendo conto dei trend attuali, potrebbe ridursi a circa il 5-6% nel 2030. Come noto il problema del cambiamento climatico interessa le complesse dinamiche dell’intera atmosfera terrestre e non può essere pertanto affrontato a scala locale o continentale, ma può essere risolto solo a scala globale.
Nonostante i timidi passi in avanti seguiti all’accordo di Parigi del 2015 e il recente ritorno dell’adesione da parte degli Stati Uniti, permane una situazione fortemente frammentata e asimmetrica a livello globale.
In questo contesto una accelerazione unilaterale da parte dell’UE, che non sia accompagnata in parallelo da un contestuale rafforzamento delle misure per evitare la rilocalizziamone delle emissioni in Paesi privi di vincoli sulle emissioni climalteranti (c.d. carbon leakage) e da un quadro di forte incentivazione agli investimenti, rischia di compromettere seriamente la competitività di settori strategici dell’industria manifatturiera europea, senza al contempo garantire alcun risultato climatico a livello globale.
È pertanto necessario che le istituzioni europee e nazionali mettano in atto una strategia industriale per governare la transizione, che contempli un ventaglio diversificato di misure agendo su molteplici fronti, non solo direttamente nel campo del clima e dell’energia, ma anche delle politiche di prodotto, del commercio, degli aiuti di stato, dell’economia circolare, della finanza. Indispensabile inoltre un supporto straordinario alla ricerca e innovazione nel campo delle tecnologie low carbon applicabili al settore siderurgico per portare gradualmente i diversi progetti in corso ad una reale implementarne su scala industriale.
Solo se l’Europa riuscirà a dimostrare che la decarbonizzazione è possibile senza che l’industria perda redditività o quote di mercato, allora altre aree del globo seguiranno il percorso dell’UE e la sfida potrà essere vinta.
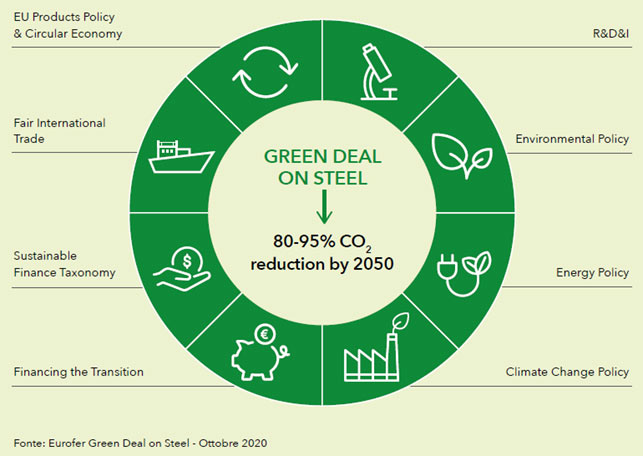
Decarbonizzazione settori hard to abate: Industrial Decarbonisation Pact.
A luglio alcune associazioni di industrie ad alta emissività hanno presentato al Governo lo studio “Strategia per la decarbonizzazione dei settori hard to abate, Industrial Decarbonisation Pact”. Dallo studio emerge che la decarbonizzazione del settore siderurgico, come quello degli altri comparti coinvolti, dipende da un approccio di sistema, in cui tutti gli attori della catena del valore devono essere coinvolti per identificare le soluzioni più efficienti Inoltre lo studio conferma, che gli obiettivi sfidanti di riduzione delle emissioni sono raggiungibili solo attraverso un portafoglio diversificato di soluzioni che include una serie di diverse possibili leve di decarbonizzazione.
Alcune di queste sono soluzioni di tipo tradizionale e quindi implementabili nel breve termine al fine di traguardare gli obiettivi al 2030, come ad esempio efficienza energetica, economia circolare, utilizzo di combustibili a minor intensità emissiva. Altre leve sono fortemente innovative e presuppongono un grande impegno in ricerca e sperimentazione nel prossimo decennio affinché i progetti pilota avviati o da avviare possano dimostrane la concreta applicabilità su scala industriale nel periodo post 2030.
Tra queste ultime si possono individuare l’utilizzo su scala industriale dei green fuel (idrogeno ma anche biometano), l’elettrificazione in sostituzione di processi di combustione ove possibile, la cattura-stoccaggio-utilizzo della CO2 (CCUS).
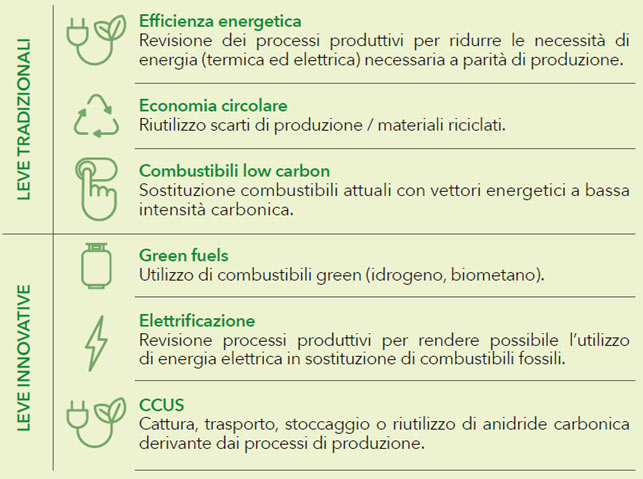
Per quanto riguarda in particolare le emissioni dirette del settore siderurgico, emerge che Green fuel e CCUS sono le leve con più alto potenziale di riduzione delle emissioni, ma allo stato attuale, in particolare con riferimento all’utilizzo dell’idrogeno, l’applicabilità è limitata e sarà necessario una fase non breve di sviluppo tecnologico e infrastrutturale per renderle strategiche ai fini di una decarbonizzazione più spinta a partire dal 2030 in poi. La tecnologia CCUS inoltre si presta ad essere adottata principalmente in grandi poli emissivi e dedicata ad evitare l’immissione in atmosfera della CO2 di processo altrimenti non eliminabile con le altre leve.
Lo studio delinea infine i requisiti chiave egli elementi abilitanti un possibile percorso di transizione verso la decarbonizzazione, a partire dalla necessità di una cornice regolatoria che consenta il mantenimento e il rafforzamento delle attuali misure di sostegno dei settori energivori, di supporto alle leve di decarbonizzazione tradizionali (efficienza energetica ed economia circolare) e di tutela dal rischio carbon leakage diretto e indiretto.
Acciaio ed economia circolare
Acciaio = materiale permanente. 100% riciclabile per cicli multipli senza perdita di proprietà.
Il ciclo siderurgico costituisce già oggi un esempio virtuoso di economia circolare applicata con successo: tutti i prodotti in acciaio raggiungono tassi di riciclo già oggi elevatissimi, con punte di eccellenza proprio nel nostro Paese. Al riciclo dei prodotti in acciaio a fine vita va aggiunto quello degli scarti o cadute di lavorazione provenienti direttamente dai processi di produzione e trasformazione dell’acciaio che vengono immediatamente reimmesse in ciclo in quantitativi prossimi al 100%.
Parlare di acciaio come di un materiale semplicemente riciclabile è oggi riduttivo: l’acciaio può essere infatti classificato come “MATERIALE PERMANENTE”.
A differenza di molti altri materiali semplicemente riciclabili, l’acciaio è un materiale durevole che può essere rifuso più e più volte senza mai perdere nessuna delle sue proprietà intrinseche quali resistenza, duttilità, formabilità, che lo rendono insostituibile in molteplici applicazioni.
I materiali permanenti devono intendersi come una nuova categoria di materiali durevoli in grado di integrare la troppo semplicistica distinzione tra materiale riciclabile e non riciclabile o tra risorsa rinnovabile o non rinnovabile. L’acciaio di cui sono fatte le costruzioni, ma anche i macchinari, le automobili e gli oggetti di uso quotidiano, rimane come valore permanentemente stoccato nella società, pronto per essere avviato al riciclo e dar così vita ad un nuovo ciclo di prodotti in acciaio, con le medesime proprietà del materiale originario.
Consumo di materie prime
I principali input di materia prima che caratterizzano la produzione di acciaio, distinta nei due cicli produttivi (ciclo integrale e forno elettrico) sono elencate di seguito.
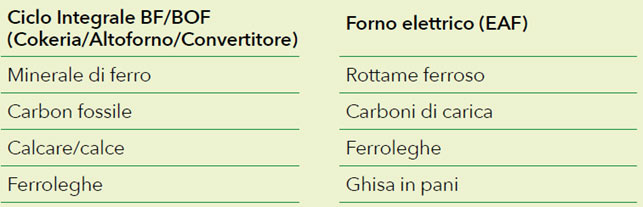
I minerali di ferro e i carboni fossili sono materiali essenzialmente di importazione che arrivano agli stabilimenti a ciclo integrale in Italia attraverso l’approvvigionamento via nave.
La materia prima principale per la produzione di acciaio a forno elettrico è invece costituita dai rottami ferrosi che derivano in parte da scarti provenienti direttamente dai processi di produzione, e in parte dai prodotti in acciaio che hanno terminato il loro ciclo di vita. L’input ferroso nel forno EAF può essere integrato anche con minerale preridotto (DRI/HBI) o pani di ghisa. I rottami provengono per circa due terzi dalla raccolta nazionale e per la rimanente parte sono importati. I rottami vengono parzialmente utilizzati anche nel convertitore a ossigeno in aggiunta alla ghisa proveniente dall’altoforno. Nel grafico seguente sono riportati l’andamento delle acquisizioni di minerale di ferro e di rottame da parte degli stabilimenti siderurgici italiani, e l’andamento della produzione complessiva di acciaio dal 2012 al 2020.
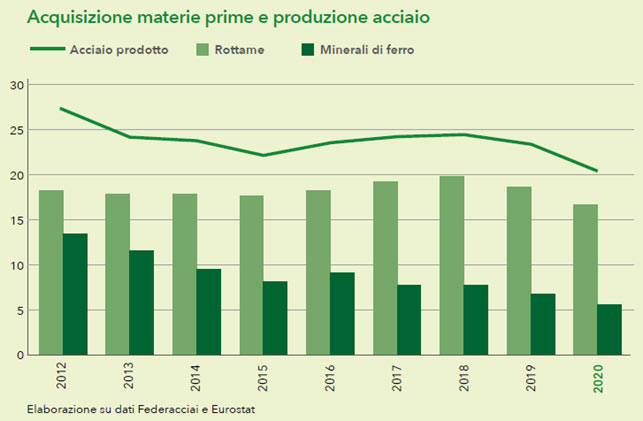
Focus sul ROTTAME FERROSO: una risorsa strategica per l’economia circolare e la decarbonizzazione
Italia primo Paese UE per il riciclo dell’acciaio.
L’Italia è il primo Paese europeo per il riciclo del rottame: nel solo 2020 le acciaierie italiane hanno rifuso circa 17 milioni di tonnellate di rottame ferroso1. Per farsi un’idea concreta della rilevanza di questo dato si può calcolare che questo quantitativo corrisponde a circa 300 volte la struttura in acciaio dell’Empire State Building di New York e si traduce in un “ritmo di riciclo” in Italia di circa 32 tonnellate di acciaio riciclato al minuto. Anche se non esistono cifre ufficiali, si stima che tassi di riciclo superiori all’80% interessino in Italia anche l’acciaio costituente i prodotti da costruzione, e quello proveniente dalle componenti di autoveicoli e dai macchinari.
Le acciaierie italiane nel 2020 hanno riciclato 32 tonnellate di acciaio al minuto.
Il riciclo virtuoso del rottame ferroso costituisce uno dei più chiari esempi a livello industriale di come si possano combinare insieme i due principali obiettivi strategici che l’UE si è data per i prossimi decenni: economia circolare e decarbonizzazione.
Il riciclo dell’acciaio, attraverso la rifusione del rottame ferroso, consente infatti evidenti benefici sia in termini di risparmio di risorse naturali che in termini energetici e di emissioni di CO2.
Per esemplificare con un numero questo concetto, si può calcolare che per ogni tonnellata di rottame di acciaio al carbonio riciclato si ottiene un risparmio di CO2 pari a 1,4 tCO2 (metodologia LCA di World Steel). Il BIR (Bureau of International Recycling) ha inoltre calcolato che il riciclo di ogni tonnellata di acciaio consente di risparmiare i seguenti input di materia e di energia.
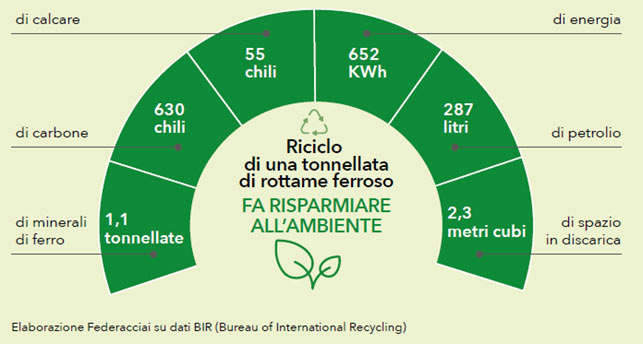
Una tonnellata di rottame riciclato consente di evitare l’emissione di 1,4 tonnellate di CO2.
Il rottame, materia prima essenziale per la produzione da forno elettrico (ma utilizzata anche parzialmente, tra il 10 ed il 15%, nel ciclo integrale), è generato sul territorio nazionale per un quantitativo di circa 15 M.t., inclusi i recuperi interni delle stesse aziende siderurgiche, e il resto del fabbisogno deve essere soddisfatto attraverso le importazioni, sia da Paesi UE che Terzi.
Mentre l’Italia necessita di importare rottame, l’Unione europea nel suo complesso è invece un netto esportatore di rottame, con esportazioni in forte aumento. Dal 2016 al 2020 le esportazioni di rottame dell’UE(28) sono aumentate sensibilmente, passando da meno di 14 M.t. del 2015 a oltre 22 M.t. nel 2020 (+64%) con un trend in continua crescita che ha raggiunto il massimo storico proprio nell’ultimo anno.
Export rottame UE +64% dal 2015
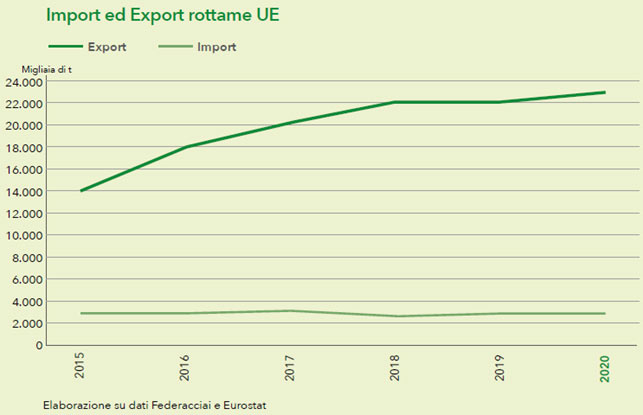
Domanda crescente di rottame: necessario aumentarne disponibilità, accessibilità e qualità in Europa.
L’ambizioso percorso di decarbonizzazione pianificato dall’UE nell’ambito del “Green Deal” (riduzione delle emissioni di gas serra del 55% al 2030 e neutralità climatica al 2050), comporterà una trasformazione radicale dell’industria siderurgica europea, che richiederà enormi investimenti in nuove tecnologie produttive, ma anche la massimizzazione dell’utilizzo di una straordinaria risorsa circolare e low-carbon come il rottame. La capacità di produzione a forno elettrico installata e la percentuale di produzione attraverso questo ciclo, in UE e nel mondo, tenderanno necessariamente a crescere, portandosi dietro una crescente domanda di rottame e in particolare di rottame con elevate caratteristiche qualitative per supportare produzioni siderurgiche a più alto valore aggiunto. In questo contesto in diversi Paesi Terzi si riscontra una tendenza alla tesaurizzazione di questa importante materia prima attraverso una serie di limitazioni commerciali all’esportazione.
Rottame ferroso: una risorsa strategica europea da difendere.
Questi scenari, unitamente alla specializzazione tecnologica e qualitativa delle produzioni siderurgiche, necessaria per resistere alla forte concorrenza extraeuropea, portano a vedere come necessarie misure che consentano di mantenere il rottame nel continente, evitando un drenaggio di risorse, pronte per essere riciclate, a vantaggio di Paesi Terzi.
Oltre il 50% dell’esportazione totale di rifiuti UE nel 2020 è costituita da rottami ferrosi.
Secondo i dati pubblicati da Eurostat il rottame ferroso costituisce di gran lunga la prima tipologia di rifiuto esportata, coprendo da sola oltre il 53% dell’intero volume di rifiuti che abbandonano l’UE. Si calcola che oltre il 20% del rottame generato in UE prenda la via di Paesi Terzi, i quali non garantiscono gli stessi standard ambientali e di sostenibilità europei (ad esempio nella gestione dei rifiuti; nella prevenzione dell’inquinamento di aria, acqua e suolo; nell’adozione delle migliori tecniche disponibili BAT, ecc.) e al contempo non hanno vincoli di riduzione della CO2 comparabili a quelli europei, con una evidente asimmetria che altera il “level playing field”. Questo fenomeno appare in netto contrasto con gli obiettivi del Programma Green Deal e del Piano d’Azione per l’Economia Circolare. Entrambi i documenti riconoscono infatti l’urgenza di porre un limite all’esportazione di rifiuti riciclabili che possono essere trattati internamente all’UE chiudendo internamente il ciclo virtuoso del recupero. Inoltre, in vari documenti, le istituzioni UE ribadiscono che la massimizzazione dell’utilizzo delle risorse secondarie generate internamente all’UE è uno dei fattori chiave non solo per preservare risorse naturali, ma anche per conseguire gli ambiziosi obiettivi UE di riduzione delle emissioni di CO2 e traguardare la neutralità climatica al 2050. Si auspica pertanto che la Commissione europea dia concreta attuazione a questi propositi con misure efficaci già a partire dalla prevista revisione del Regolamento sul trasporto transfrontaliero di rifiuti (Waste Shipment Regulation).
È inoltre di fondamentale importanza che l’intera filiera di fornitura del rottame sia orientata a migliorare la disponibilità, l’accessibilità e soprattutto le caratteristiche qualitative del rottame. Un impulso allo sviluppo dell’ecodesign nella progettazione di prodotti che contengono parti in acciaio può contribuire a migliorare la possibilità di disassemblaggio o separazione della componente ferrosa a fine vita, contribuendo ad incrementare i tassi di recupero (già peraltro molto elevati). Allo stesso modo è necessario promuovere le iniziative di ricerca e innovazione finalizzate a migliorare le tecnologie di recupero, di preparazione e selezione del rottame per minimizzare la presenza di sostanze estranee o indesiderate, contribuendo a migliorare la qualità della materia prima in ingresso alle acciaierie e conseguentemente l’efficienza e il risparmio di materia ed energia.
Gestione dei residui
Tra i punti che distinguono la circolarità di un ciclo produttivo c’è la capacità di trasformare al meglio le materie prime in ingresso minimizzando la quantità di scarti prodotti, valorizzare al meglio le qualità degli stessi per un successivo riuso e ridurre i rifiuti destinati allo smaltimento.
Oltre il 90% in peso dei rifiuti è classificabile come “non pericoloso”.
I processi di produzione dell’acciaio comportano inevitabilmente la generazione di quantitativi importanti di scarti e residui. Tuttavia la maggior parte di tali materiali, in considerazione delle proprietà fisiche e della composizione chimica che possiedono, risulta in molti casi adatta ad essere valorizzata e riutilizzata sia direttamente all’interno dello stesso processo, sia in altri ambiti industriali. Si può stimare che oltre il 90% in peso dei rifiuti complessivamente prodotti dalla siderurgia è classificato come rifiuto speciale “non pericoloso”. L’indicatore di World Steel per la “material efficiency” riporta valori per la siderurgia che si attestano negli ultimi anni intorno al 97%. Tale indicatore mostra come solo il 3% in peso delle materie prime è inevitabilmente destinato a tramutarsi in rifiuto da avviare allo smaltimento.
Nella gerarchia delle azioni virtuose in tema di gestione dei rifiuti il primo posto è occupato dalla prevenzione della generazione stessa dei residui. L’analisi del campione di riferimento di aziende, limitato alla produzione di acciaio da forno elettrico, evidenzia come negli ultimi 8 anni si sia ridotta del 22% la produzione specifica di rifiuti, pari a oltre 43 kg di rifiuti in meno per ogni tonnellata di acciaio prodotta.
Produzione di rifiuti per t di acciaio -22% dal 2012 -9% dal 2017
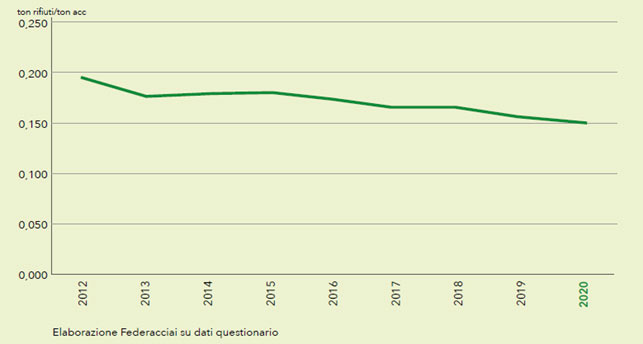
Il 72% dei rifiuti prodotti in siderurgia vengono avviati a recupero.
Per quanto riguarda invece la gestione e destinazione del rifiuto a valle della sua generazione i principi dell’economia circolare impongono di massimizzarne il riciclo e il recupero, minimizzando il ricorso allo smaltimento.
Sulla base dei dati rilevati dal campione di riferimento di aziende che hanno risposto al questionario, si osserva come nel suo complesso il settore (processo di produzione e processi di trasformazione acciaio) negli ultimi 4 anni abbia fatto registrare un aumento del 13% dei rifiuti destinati al recupero, che si attestano nel 2020 al 72%.
Rifiuti avviati a recupero +13% dal 2017
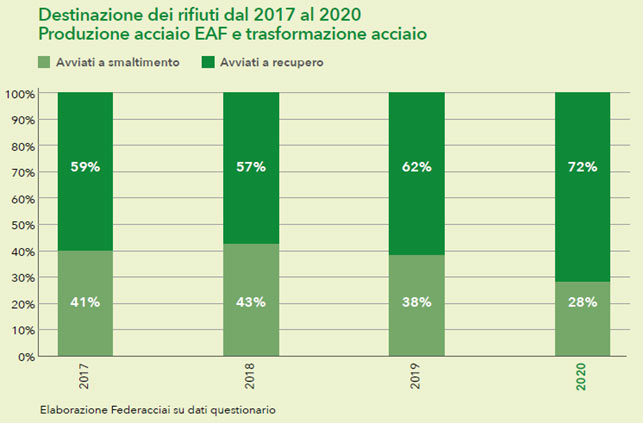
Tale miglioramento è dovuto in particolare alle prestazioni registrate dagli impianti di produzione acciaio, che nel 2020 hanno inviato a recupero il 67% dei rifiuti prodotti, mentre per i processi di trasformazione nello stesso anno i rifiuti a recupero si sono confermati al 93%.
Se si analizzano nel dettaglio le singole tipologie di rifiuto associate alla produzione di acciaio e in particolare la loro potenzialità di recupero già oggi possibile si evidenzia come il ricorso alla discarica sia purtroppo ancora troppo elevato e ci siano margini per ulteriori riduzioni. A questa situazione contribuisce in maniera non trascurabile l’incertezza normativa a livello nazionale in tema di recupero di rifiuti, con particolare riferimento all’applicazione della norma sulla cessazione dello status di rifiuto (c.d. End of Waste) o all’attribuzione dello status di sottoprodotto. Questa criticità si è accentuata negli ultimi anni, impedendo ad imprese, enti competenti e di controllo di muoversi in un quadro di regole certe, a discapito dello sviluppo dell’economia circolare.
La simbiosi industriale
La simbiosi industriale si fonda infatti sulla possibilità di uno scambio di risorse tra due o più industrie di settori diversi, intendendo con il termine “risorse” tanto i materiali (sottoprodotti o rifiuti), quanto i cascami energetici, i servizi o altro, attraverso soluzioni che possono risultare vantaggiose per entrambi i soggetti.
Si tratta, in estrema sintesi, di sinergie di tipo “win-win” che possono svolgere un ruolo molto importante nello sviluppo dell’economia circolare. I vantaggi ambientali derivanti dalla valorizzazione dei residui, sia recuperati internamente sia destinati ad altri processi di produzione o utilizzo, sono quindi evidenti:
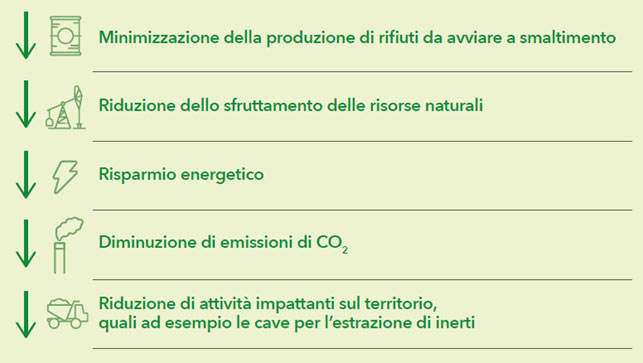
Si riportano di seguito le principali possibilità di valorizzazione dei residui dei processi di produzione siderurgica già oggi consolidate o tecnicamente possibili.
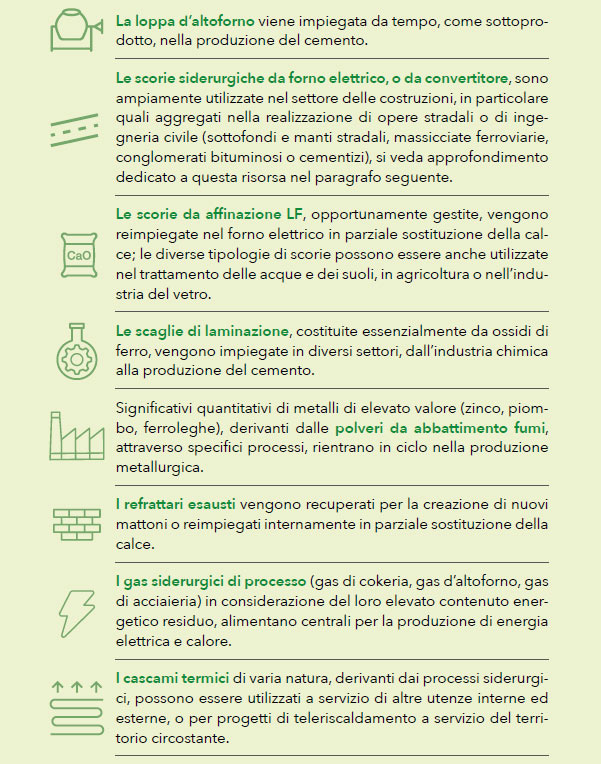
Inoltre il processo di produzione di acciaio, oltre a realizzare pienamente il riciclo dei materiali ferrosi derivanti da molteplici usi finali o di processo, può consentire a certe condizioni anche di accogliere materiali di altri natura (ad esempio materiali di derivazione plastica) in parziale sostituzione di materiali carboniosi, con vantaggi tangibili sia in termini di contributo alla circolarità degli scarti più difficilmente riciclabili (plastiche), sia in termini di riduzione delle emissioni di CO2.
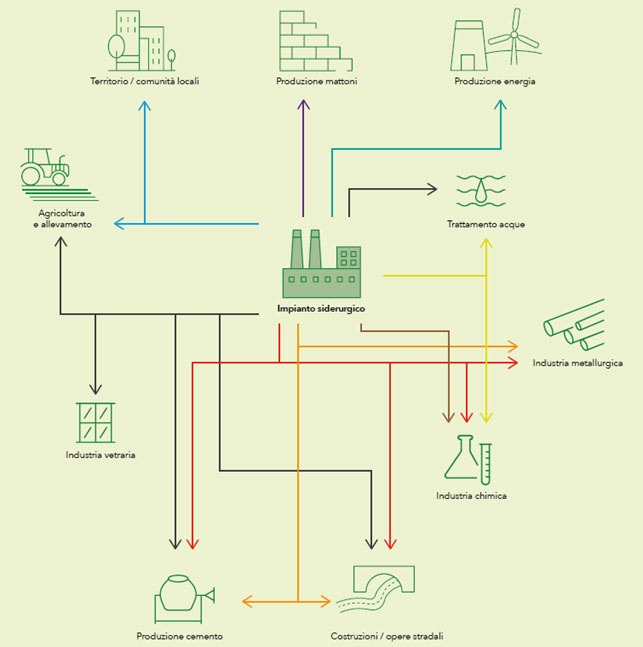
Focus sulla SCORIA SIDERURGICA: una risorsa sicura e sostenibile per la simbiosi industriale.
Le scorie siderurgiche, se opportunamente gestite, hanno dimostrato di essere un’ottima risorsa sostitutiva dei prodotti derivanti dalle risorse naturali sia dal punto di vista tecnico/prestazionale che ambientale.
Le scorie siderurgiche (loppa da altoforno, scoria da convertitore, scorie da forno elettrico) rappresentano, in termini quantitativi, il principale residuo derivante dalla produzione di acciaio e, se opportunamente gestite, possiedono caratteristiche tali da poter trovare valido impiego in altri e differenti ambiti. Le scorie siderurgiche hanno dimostrato infatti di essere un’ottima risorsa sostitutiva, o complementare, dei prodotti derivanti dalle risorse naturali, sia dal punto di vista tecnico/prestazionale che ambientale. Il loro impiego sostenibile risponde pertanto appieno agli obiettivi dell’Economia Circolare e della simbiosi industriale.
Del resto, la stessa Commissione europea, nella sua Comunicazione COM(2007)59 interpretativa in materia di rifiuti e sottoprodotti, aveva già individuato esplicitamente sin dal 2007 la loppa da altoforno, generata dalla produzione siderurgica a ciclo integrale, tra gli esempi concreti di materiali classificabili come sottoprodotto utilizzabile nella produzione del cemento, in sostituzione, o a complemento, delle materie prime vergini. La valorizzazione delle scorie come risorse e la necessità di superare un approccio basato sulla gestione di un rifiuto “di cui disfarsi”, ha portato l’industria siderurgica– a livello europeo e nazionale – a intraprendere la strada della registrazione ai sensi del Regolamento REACH (Regolamento UE destinato alle sostanze, miscele e articoli immessi sul mercato e non applicabile ai rifiuti). Nel “Rapporto sulla Sicurezza Chimica” (CSR), previsto dalla registrazione REACH, sono riportate le conclusioni derivanti dalla caratterizzazione delle scorie siderurgiche per quanto attiene non solo gli aspetti chimico-fisici, ma anche quelli eco-tossicologici e tossicologici. E il CSR conclude che la scoria non è classificata ai fini del Sistema Globalizzato di Classificazione ed Etichettatura delle Sostanze Chimiche (GHS), e della Direttiva per le sostanze pericolose, e pertanto non le sono attribuite caratteristiche di pericolosità.
Focalizzando l’analisi sul ciclo produttivo da forno elettrico (EAF) – in termini generali – sono essenzialmente due le tipologie di scoria che si originano da tale processo, comunemente chiamate “scoria nera”, che si forma sopra il bagno di fusione del rottame ferroso, e “scoria bianca”, derivante dalla fase di affinazione fuori forno dell’acciaio, che avviene in siviera.
Si tratta di materiali aventi composizione, caratteristiche e proprietà differenti, e che pertanto trovano impieghi differenti.
Una recente indagine (2019) sulla scoria nera e sulla scoria bianca prodotte in Regione Lombardia, ha messo bene in luce quale sia appunto il potenziale e differente utilizzo di tali materiali.
La scoria nera generata dal processo di fusione (mediamente 0,15-0,20 t di scoria per t di acciaio) ha un utilizzo consolidato (come “Sottoprodotto” o “End of Waste”) in sostituzione degli inerti naturali nel settore delle costruzioni, sia come aggregato non legato (rilevati e sottofondi stradali, massicciate ferroviarie, ecc.), che legato (conglomerati bituminosi e cementizi, manti di usura, ecc.).
I dati 2019 evidenziano tuttavia che purtroppo ancora il 27% della scoria nera EAF prodotta in Lombardia è destinato a smaltimento in discarica, con una percentuale decisamente superiore a quanto avviene mediamente in UE (sulla base dei dati di EUROSLAG la percentuale di scoria di acciaieria destinata a smaltimento in discarica nei principali Paesi UE è stimabile intorno al 15%).
La scoria bianca è generata dal processo di affinazione dell’acciaio ed è prodotta in quantitativi proporzionalmente minori rispetto alla scoria nera (0,03-0,05 t di scoria per t di acciaio). Allo stato attuale i dati evidenziano tuttavia che la quasi totalità della scoria bianca è destinata in discarica per inerti (oltre il 94% nel 2019). Si stanno attualmente sperimentando diverse possibilità di recupero: il residuo, se opportunamente gestito, presenta infatti caratteristiche chimico/fisiche tali da poter essere utilizzato come sostituito della calce nello stesso processo siderurgico, nei cementifici o in altre applicazioni. Alcune criticità sono legate alla granulometria particolarmente fine del residuo, in grado di generare elevata polverosità.
A questo riguardo si stanno studiando processi di trattamento con granulazione ad aria, che permettano di separare efficacemente la scoria dal metallo residuo e di prevenire la generazione di emissioni diffuse senza l’utilizzo di acqua.
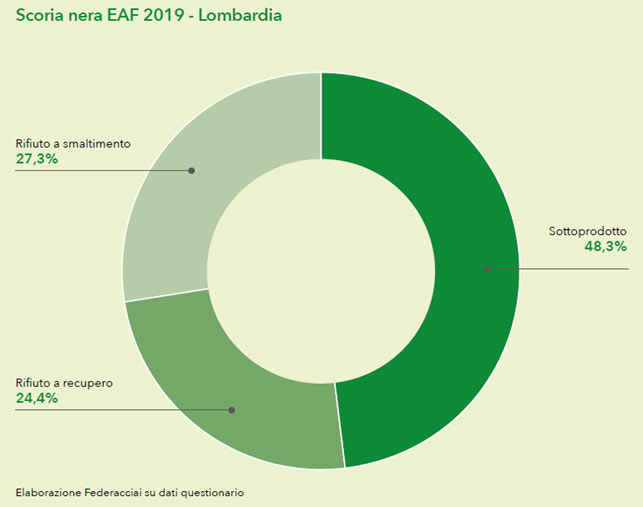
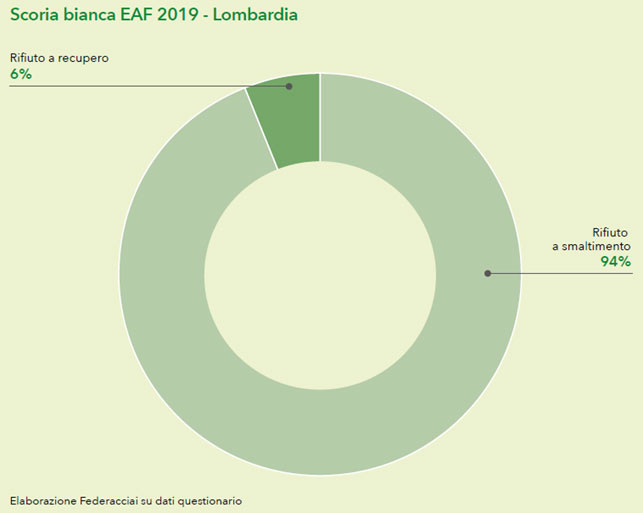
Prevenzione dell’inquinamento atmosferico
L’applicazione da parte delle imprese siderurgiche delle migliori tecnologie disponibili in termini di prevenzione e di abbattimento delle emissioni in aria, nonché i costanti progressi nelle procedure di controllo e monitoraggio dei parametri di processo e i miglioramenti nella gestione delle materie prime, hanno portato negli anni ad una drastica riduzione delle emissioni in aria per tutti i principali inquinanti oggetto di indagine.
Questi risultati sono testimoniati dalle serie storiche pubblicate annualmente da ISPRA nella sezione dedicata alla siderurgia dell’“Annuario dei dati ambientali”, che riporta l’andamento delle emissioni specifiche (inquinante emesso/ acciaio prodotto) per una serie di parametri. Si riportano di seguito i dati riferiti a due dei principali inquinanti derivanti dai processi di combustione (NOx, SOx) a partire dal 1990 fino al 2018, ultimo dato disponibile nell’annuario ISPRA 2020.
NOx -66% dal 1990 -32% dal 2010
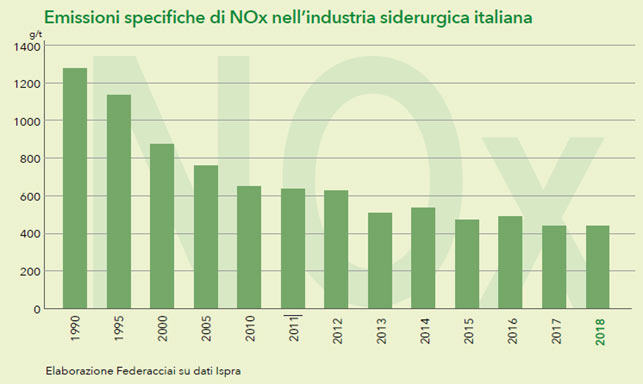
SOx -88% dal 1990 -40% dal 2010
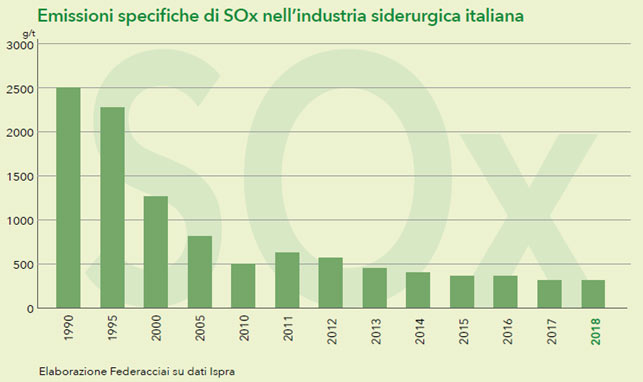
Sulla base dei dati pubblicati da ISPRA le emissioni specifiche di NOx e SOx per tonnellata di acciaio prodotto si sono ridotte drasticamente dal 1990 in poi. Considerando solo l’ultimo decennio le emissioni specifiche di NOx della siderurgia italiana si sono ridotte di oltre il 30% e quelle di SOx di circa il 40% rispetto al 2010.
Miglioramento continuo nell’abbattimento delle emissioni tramite applicazione delle BAT.
Con particolare riferimento alle emissioni di NOx, i risultati sono ottenuti grazie all’impiego di nuovi e più efficienti forni di riscaldo e bruciatori e ad un miglior controllo dei processi di combustione.
Un ulteriore e impegnativo sforzo di riduzione delle emissioni di NOx sarà richiesto agli impianti dall’applicazione delle nuove Conclusioni BAT per il settore “Ferrous Metal Processing” (FMP BAT Conclusions) che saranno formalmente adottate dalla Commissione europea nel 2022 e la cui piena implementazione è attesa entro il 2026.
Risultati molto significativi sono stati raggiunti dalle acciaierie italiane anche nell’abbattimento delle emissioni di polveri. Questo inquinante, anche in considerazione degli obiettivi generali di qualità dell’aria e della conformazione geomorfologica delle aree dove sono situate la maggior degli stabilimenti a forno elettrico italiani (pianura padana), è stato oggetto della massima attenzione da parte delle autorità competenti e di controllo e ha costituito il principale target degli interventi messi in atto dalle acciaierie, che oggi sono tutte dotate dei più moderni ed efficienti sistemi di captazione, aspirazione e filtrazione dei fumi. Queste soluzioni tecnologiche, nonché l’adozione di sistemi di monitoraggio in continuo delle prestazioni e dei parametri ad esse correlate, consentono oggi di raggiungere performance molto elevate in termini di abbattimento delle polveri al camino e il rispetto di limiti molto stringenti fissati dalle AIA, che in alcuni casi si spingono oltre le prestazioni indicate a livello UE nelle conclusioni BAT.
I risultati raggiunti nell’abbattimento delle emissioni di polveri (inquinante non rendicontato in maniera dedicata per il comparto siderurgico nell’annuario ISPRA) sono testimoniati dalla raccolta dati effettuata da Federacciai a partire dal 2008 su un campione largamente rappresentativo della produzione di acciaio da forno elettrico. I risultati evidenziano una drastica riduzione legata all’implementazione delle BAT seguita negli anni più recenti da un consolidamento dei risultati raggiunti.
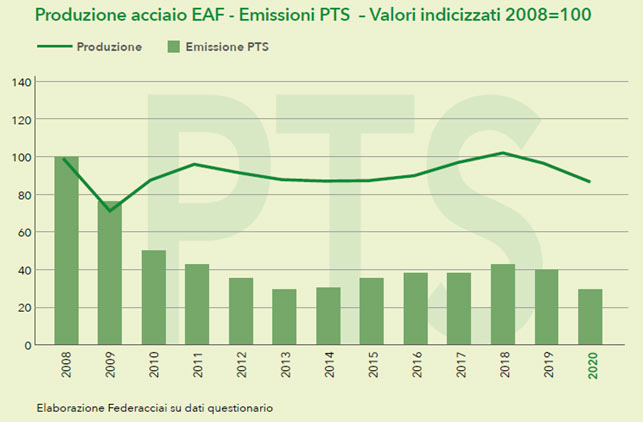
Polveri (PTS) -64% dal 2008
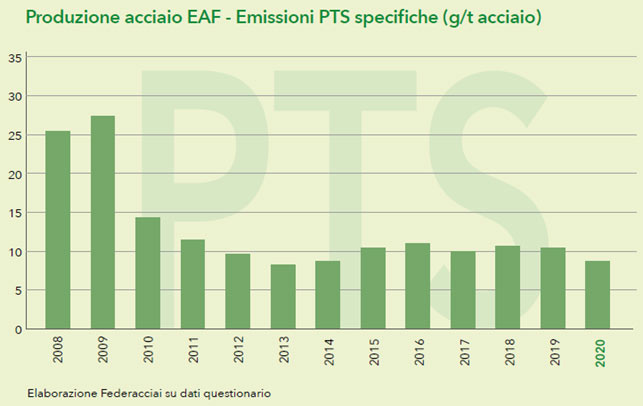
Secondo l’indagine condotta da Federacciai su un campione rappresentativo di impianti EAF a partire dal 2008, le emissioni specifiche di polveri totali sospese (PTS) delle acciaierie a forno elettrico italiane si sono ridotte di oltre il 60%.
Monitoraggio in continuo delle prestazioni dei sistemi di abbattimento.
Tutti gli interventi mirati all’abbattimento delle concentrazioni di polveri al camino hanno inoltre contribuito in maniera determinante anche alla minimizzazione delle emissioni di altri inquinanti che sono correlati alla concentrazione di polveri, come i metalli pesanti e i microinquinanti organici.
In particolare negli impianti elettrosiderurgici, l’installazione dei sistemi di insufflazione di carboni attivi nel condotto a monte del filtro, unitamente ad un miglior controllo dei parametri di processo e delle materie prime, misure implementate su larga scala dalle acciaierie negli ultimi anni, ha consentito di abbattere in maniera efficace le concentrazioni di diossine e furani (PCCD/F), come confermato anche da diverse indagini e studi condotti dagli enti di controllo a livello locale1.
Un ruolo determinante ha anche assunto l’adozione di buone pratiche di gestione, manutenzione e controllo degli impianti volte a garantire il mantenimento costante di prestazioni elevate, anche attraverso il monitoraggio in continuo delle emissioni e di alcuni parametri correlati alla efficienza di aspirazione o alla prestazione dei filtri che consente di verificare l’insorgere di situazioni di deriva e di intervenire in maniera tempestiva e mirata.
Tutela della risorsa idrica
Elevata percentuale di ricircolo delle acque di raffreddamento, con valori medi del 77% e punte fino al 98%.
L’interazione con il territorio e l’uso razionale della risorsa idrica sono aspetti molto importanti per il l’obbiettivo di un’economia pulita e circolare.
Nei processi siderurgici l’acqua trova il suo maggiore impiego nel raffreddamento dei macchinari e nel raffreddamento/condizionamento di materie prime, prodotti della lavorazione e materiali di scarto. Con riferimento all’uso della risorsa idrica, il ciclo di lavorazione non necessita di acque di qualità elevata e i prelievi dagli acquedotti sono molto limitati e circoscritti essenzialmente agli usi civili.
Va inoltre considerato che una parte dell’acqua prelevata, impiegata quale fluido freddo negli scambiatori termici (raffreddamento indiretto), viene restituita all’ambiente senza avere subito di fatto nessuna contaminazione.
L’altra acqua utilizzata nei siti, viene rilasciata nell’ambiente in forma di vapore oppure avviata allo scarico, dopo gli opportuni trattamenti chimicofisici. In una misura molto ridotta accompagna fanghi ed altri materiali di risulta.
Il ricorso ai più efficienti sistemi di raffreddamento (con sistemi che mediamente garantiscono il 77% del ricircolo delle acque e che si spingono fino al 98%) ha permesso al settore di migliorare le performance nell’utilizzo della risorsa idrica.
Dal 2010 al 2020 riduzione di circa 2.7 mc di acqua prelevata su tonnellata di acciaio prodotto.
Sebbene l’andamento dei prelievi specifici risulti influenzato dalle prodizioni di acciaio – in particolare le prestazioni dei sistemi di raffreddamento risultano ottimali al crescere delle produzioni di acciaio – facendo registrare delle oscillazioni nel corso degli anni, i dati del campione di riferimento degli impianti di produzione acciaio a forno elettrico, evidenziano come negli ultimi 11 anni (dal 2010 al 2020) i prelievi specifici di acqua siano complessivamente scesi di oltre il 17%; il confronto tra il 2010 e il 2020 (anni con produzioni paragonabili) fa registrare una riduzione di circa 2.7 m3 di acqua prelevata su tonnellata di acciaio prodotto.
Dal 2010 al 2020 -17,58%
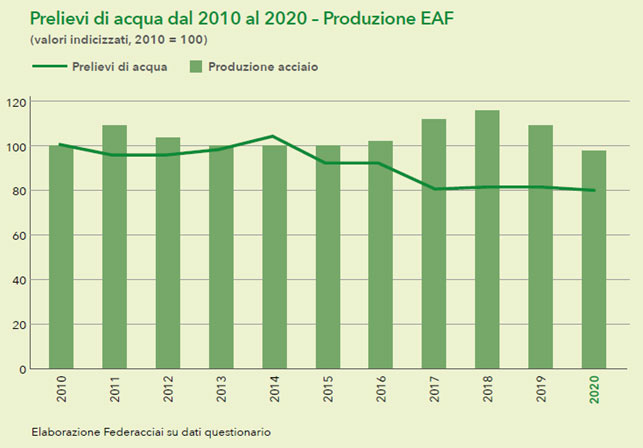
La scelta delle fonti di approvvigionamento e delle migliori soluzioni tecniche per i sistemi di raffreddamento è influenzata in modo significativo dalla localizzazione e dalle condizioni climatiche dei siti. Gli impianti a ciclo integrale, situati in zone costiere, attingono soprattutto dal mare le acque impiegate per il raffreddamento indiretto degli impianti; gli impianti a forno elettrico, tipicamente situati in zone interne del territorio, impiegano acque prelevate principalmente dai corpi idrici superficiali.
Il grafico seguente mostra la distribuzione percentuale delle fonti di prelievo, relativa al campione di riferimento degli impianti di produzione acciaio a forno elettrico.
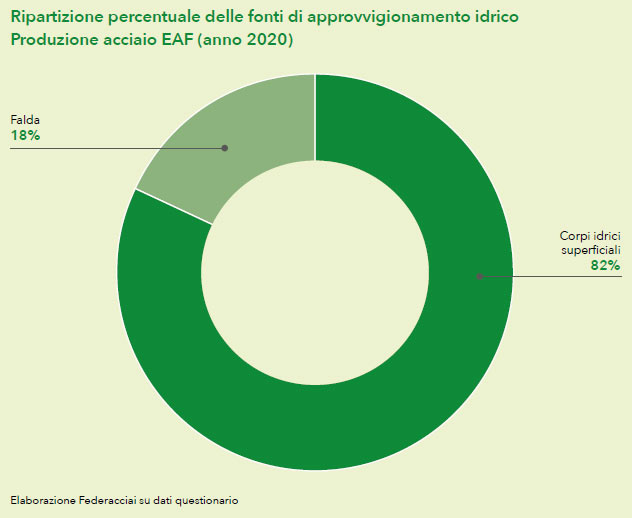
Risorse energetiche
Nei piani di sviluppo europei e nazionali che fanno della transizione ecologica uno dei pilastri per la crescita dei prossimi anni, ricopriranno un ruolo fondamentale l’efficientamento energetico, la produzione di energia da fonti rinnovabili, l’armonizzazione delle reti e dei mercati energetici europei per un efficiente e sicuro utilizzo delle risorse. Questi importanti traguardi richiederanno sempre ulteriori impegni all’industria siderurgica, che dovrà confrontarsi nel breve/medio termine con le strategie di miglioramento tecnologico/impiantistico e di gestione efficiente delle risorse energetiche ma sempre di più dovrà confrontarsi nel medio/lungo periodo con impegnativi progetti di trasformazione dei processi produttivi. Tali sforzi necessiteranno di importanti strumenti di sostegno finanziario da parte delle istituzioni europee e nazionali.
La siderurgia italiana si presenta di fronte a queste nuove sfide avendo già raggiunto importanti risultati in termini di efficienza energetica e uso razionale della risorsa.
Le elaborazioni svolte dalla Commissione europea nell’ambito del progetto ODYSSEE evidenziano che dal 1995 ad oggi la siderurgia italiana, grazie alla continua innovazione dei propri impianti e all’introduzione di sistemi di gestione energetica sempre più efficienti, ha ridotto di circa il 36% i propri consumi energetici totali per tonnellata di acciaio prodotto.
-35,7% dal 1995 -33,3% al 2000
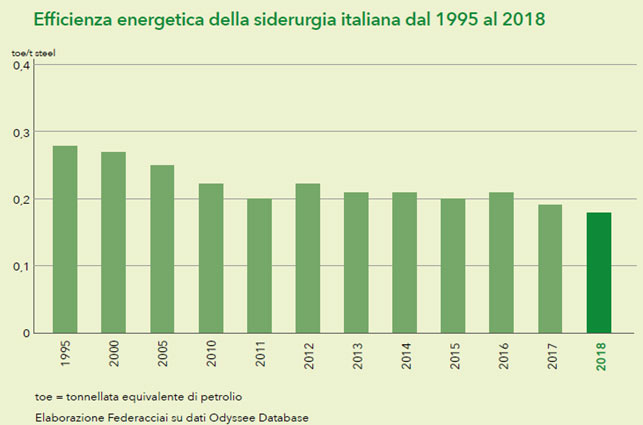
La siderurgia italiana si presenta di fronte alle nuove sfide della transizione ecologica avendo già raggiunto importanti risultati.
Il valore della prestazione in termini di consumo energetico unitario della siderurgia (tonnellate equivalenti di petrolio per tonnellata di acciaio prodotto) rappresenta sia il livello raggiunto di efficienza energetica propriamente detta (uso delle tecnologie e gestione energetica) sia la ripartizione tra i due cicli produttivi (ciclo integrale e forno elettrico), aspetto quest’ultimo che vede l’Italia distinguersi dai principali produttori europei per una netta prevalenza percentuale di produzione a forno elettrico.
Siderurgia italiana prima in Europa per efficienza energetica.
La siderurgia italiana ha continuamente migliorato le proprie prestazioni, confermandosi negli ultimi anni come la più efficiente rispetto alle principali siderurgie europee, con consumi specifici nel 2018 pari a 0,18 toe/t steel ampiamente al di sotto della media europea e dei principali competitor di Germania, Francia e Inghilterra.
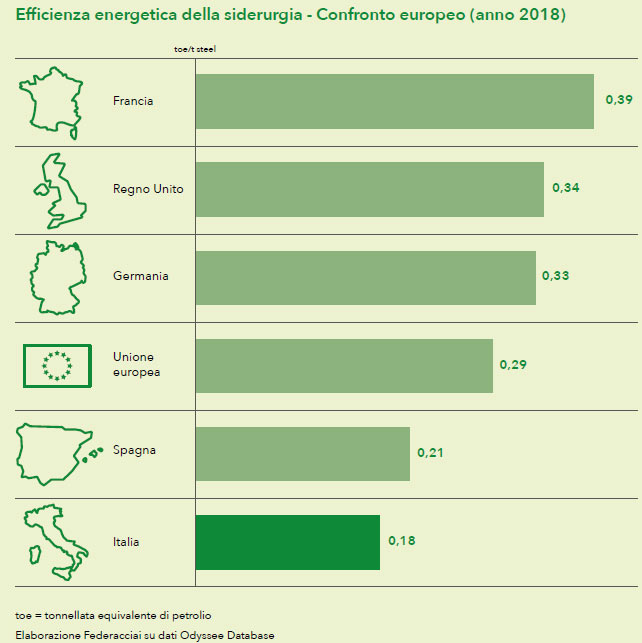
Efficienza energetica Italia +38% rispetto alla media europea.
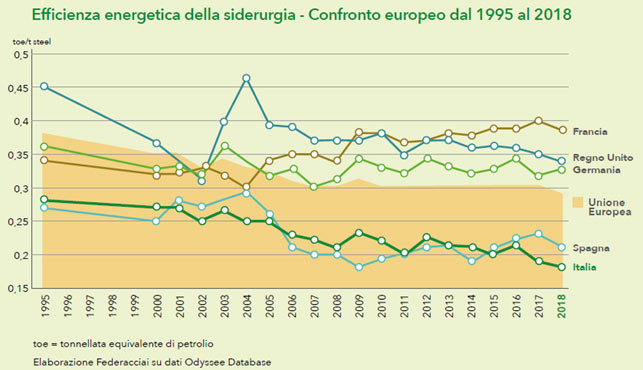
Rivoluzione verde e transizione energetica: sviluppo efficiente delle fonti rinnovabili per garantire ai consumatori industriali l’accesso all’energia green a condizioni competitive.
Per la riuscita della “rivoluzione verde”, individuata come missione dal PNRR, un ruolo importante sarà ricoperto dallo sviluppo efficiente delle fonti rinnovabili all’interno del mercato nazionale ed europeo, in grado di garantire ai consumatori industriali l’accesso all’energia green a condizioni competitive.
Le aziende siderurgiche italiane, oltre agli investimenti messi in campo già da anni per l’installazione di impianti per l’autoproduzione/autoconsumo di energia elettrica da fonti rinnovabili all’interno dei siti industriali (utilizzo dei tetti dei capannoni, recupero e conversione di aree dismesse e bonificate, recupero di calore dai fumi con ORC, ecc.) negli ultimi 2 anni sono state le prime tra le industrie energivore ad avere sottoscritto contratti di fornitura in forma di Power Purchase Agreement (PPA). Se per il momento si tratta ancora di pochi casi e con limitata copertura dei consumi elettrici totali, lo sviluppo in larga scala di questi strumenti rappresenterebbe una valida leva di sviluppo della produzione da fonti rinnovabili per l’intero settore elettrico. Per questo è necessario che il settore venga regolato, e non lasciato a sole logiche di mercato, e che vengano introdotti in particolare strumenti di copertura del rischio a termine dell’energia come l’introduzione di un fondo in grado di equilibrare i picchi e le cadute dei prezzi.
Consumi energetici dell’industria siderurgica italiana
Se si analizzano i soli consumi elettrici del settore, negli ultimi anni si registra un lieve e costante miglioramento delle prestazioni, che sembrerebbe dimostrare come il settore stia assimilando i nuovi assetti produttivi, che vedono la crescita della produzione da forno elettrico, che rappresenta la tecnologia con i consumi maggiori di energia elettrica, rispetto alla produzione a ciclo integrale.
I consumi specifici di gas naturale deli ultimi anni evidenziano una sostanziale stabilità del parametro sull’intorno degli 80 mc/ton di acciaio.
Sulla base dei dati rilevati dal campione di aziende che hanno risposto al questionario, è stata predisposta un’analisi di dettaglio dei consumi nei forni elettrici ad arco, impianti e apparecchiature nei confini di impianto fino alla colata e nei processi di trasformazione a caldo (forni di riscaldo, trattamento, ecc.), processi che maggiormente impiegano rispettivamente i vettori energia elettrica e gas naturale.
L’andamento degli ultimi 4 anni mostra una riduzione dei consumi specifici in entrambe le situazioni, evidenziando come il corretto monitoraggio delle risorse energetiche effettuato dalle aziende siderurgiche permetta di indirizzare al meglio gli interventi di efficientamento negli impianti.
A tal proposito le prime risultanze sul secondo ciclo di obbligo delle diagnosi energetiche presentate da ENEA, hanno evidenziato come degli oltre 200 siti produttivi che hanno presentato una diagnosi energetica nel dicembre del 2019 oltre il 70% applica il monitoraggio dei consumi energetici in conformità alle Linee Guida di ENEA e circa il 15% adotta un sistema di gestione certifica ISO 50001.
L’adozione delle migliori tecniche disponibili in campo ambientale (BAT)
Il settore siderurgico è soggetto alla disciplina comunitaria in materia di prevenzione e controllo integrato dell’inquinamento (introdotta nel 1996) i cui principi sono stati rafforzati a seguito della pubblicazione della Direttiva in materia di emissioni industriali (IED – Industrial Emissions Directive, Dir. 2010/75/UE, recepita in Italia dal D.Lgs. n. 46/2014) che ha assegnato un ruolo fondamentale alle c.d. “Conclusioni BAT” che costituiscono oggi l’atto di riferimento vincolante per le autorità competenti degli Stati membri ai fini della fissazione delle condizioni e delle prescrizioni (inclusi i limiti di emissione) nelle Autorizzazioni Integrate Ambientali (AIA) dei singoli impianti.
Le BAT (Best Available Techniques) applicabili per ciascun aspetto ambientale (emissioni in atmosfera, scarichi idrici, gestione dei rifiuti, risparmio energetico, ecc.) e per ciascuna tipologia di processo produttivo sono individuate e descritte all’interno di un documento di riferimento settoriale denominato BRef (BAT Reference) che viene elaborato dall’European IPPC Bureau della Commissione europea a seguito di un confronto tecnico che vede la partecipazione di esperti nominati dagli Stati membri e dall’industria. Il BRef viene periodicamente aggiornato per tenere conto dei progressi nelle tecniche esistenti o di nuove tecniche applicabili.
Dal 2026 saranno operative anche le nuove conclusioni BAT per la trasformazione acciaio.
Il confronto tecnico costante a livello nazionale ed europeo che vede il coinvolgimento diretto delle imprese interessate e le autorità competenti rappresenta uno dei punti di forza della disciplina IPPC/IED.
Le aziende sono in questo modo sottoposte ad un continuo aggiornamento tecnico dei propri impianti per adeguarsi alle BAT e alle relative prestazioni, e ridurre i propri impatti sull’ambiente attraverso un approccio integrato e in un’ottica di miglioramento continuo.
Con l’applicazione delle BAT i processi siderurgici garantiscono livelli di tutela ambientale tra i più stringenti a livello mondiale
Con l’entrata in operatività nel 2016 delle “Conclusioni BAT” per i processi di produzione di ghisa e acciaio, il settore siderurgico è stato il primo comparto industriale europeo in ordine di tempo, ad avere un documento di tale natura in conformità alle più recenti e stringenti disposizioni in materia di emissioni industriali e prevenzione dell’inquinamento (IED); con il completamento nel 2022 della revisione del BRef dedicato alla trasformazione acciaio, tutti i principali processi siderurgici soggetti ad IPPC saranno vincolati, nei termini previsti dalla normativa, al raggiungimento dei livelli di emissione BAT individuati a livello comunitario, garantendo un livello di tutela che è tra i più stringenti a livello mondiale.
L’adozione di sistemi di gestione ambientale
Se da un lato, infatti, la certificazione ISO 14001 consente all’azienda di aumentare la considerazione e l’opinione da parte degli stakeholder (consumatori, utenti finali, clienti, fornitori, autorità di controllo, ecc.), “garantendo che tutte le fasi dalla progettazione alla distribuzione, fino allo smaltimento vengano controllate o influenzate dall’impresa certificata”, dall’altro, proprio grazie all’impegno messo in campo per il conseguimento degli obiettivi ambientali previsti dalla certificazione, si ha in molti casi “un incremento di produttività e di riduzione di costi per l’impresa”.
I dati resi disponibili nella banca dati di Accredia non fanno che confermare tali riflessioni, e non sorprende quindi che, per il settore metallurgico, la certificazione ambientale ISO 14001 rappresenti la certificazione più diffusa tra le imprese dopo quella di qualità ISO 9001.
Oltre 2.500 certificazioni ambientali ISO 14001 nell’industria dei metalli
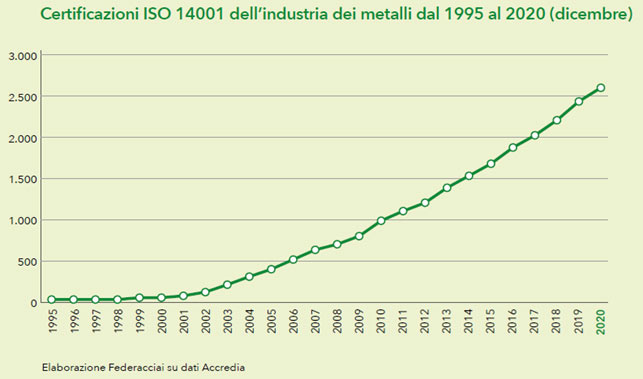