Ponti a travata
Ponti a travata
PRINCIPALI CARATTERISTICHE DEI PONTI A TRAVATA
I ponti a travata costituiscono la più comune e semplice tipologia strutturale impiegata per coprire le luci minori. In assenza di vincoli sulla posizione delle pile, la distanza tra gli appoggi è compresa tra 40 e 80 m.
I ponti a travata si distinguono in due schemi statici comunemente utilizzati:
- Travi in semplice appoggio
- Trave continua su più appoggi
Quest’ultima soluzione consente di ridurre sia il numero di apparecchi di appoggio (-50% negli appoggi centrali), elementi costosi soprattutto in termini di manutenzione e che occupano uno spazio consistente sulle pile e pertanto richiedono pulvini di dimensione maggiore, sia il quantitativo di giunti (deformazione concentrata dunque in pochi punti), riducendo la manutenzione stradale.
I ponti a travata continua hanno inoltre un miglior del comportamento sotto le azioni sismiche.
Tenendo presenti tutti questi vantaggi, è importante ricordare che queste soluzioni necessitano di una maggiore attenzione per le fasi di varo e l’assemblaggio dei conci.
Sempre nel caso di schema statico a trave continua, è conveniente che le campate laterali siano realizzate con luci pari all’80% delle campate centrali, in modo da avere sollecitazioni simili fra loro.
Solitamente i ponti travata comportano i seguenti vantaggi rispetto alle equivalenti soluzioni in cemento armato precompresso:
- Leggerezza (elevato rapporto resistenza/peso), venendo incontro alle tipiche problematiche di carattere logistico e sismico, avendo un tonnellaggio di gran lunga inferiore, ma anche riducendo le opere di fondazione;
- Rapidità e facilità di esecuzione di impalcati continui, grazie alla facilità di giuntare in opera i vari conci di trave;
- Facilità di manutenzione: se ben protetto un ponte in acciaio ha un’ottima durabilità. Qualora dovessere insorgere problematiche di corrosione o di ammaloramento, il sistema costruttivo in acciaio consente una più agevole osservazione e ispezione degli elementi strutturali rispetto ad una soluzione in calcestruzzo dove, in quest’ultimo caso, di fatto il problema lo si riscontra ormai quando la corrosione delle barre o dei cavi è già in fase avanzata.
Gli interventi di ripristino sono inoltre più facili da eseguire rispetto ai ponti in c.a.;
- Sfruttamento del comportamento a sezione mista acciaio-calcestruzzo, essendo impiegata solitamente una soletta in calcestruzzo;
- Adattabilità alle luci ed alla geometria del tracciato stradale;
- Scarsa sensibilità ai cedimenti differenziali delle fondazioni;
- Qualità architettonica conferita dalla semplicità dei particolari costruttivi.
I ponti a travata sono solitamente convenienti per campate fino a 150 m. Luci maggiori devono essere giustificate da opportune condizioni al contorno.
Il ponte a travata più lungo al mondo si trova a Rio de Janeiro e raggiunge una luce massima fra gli appoggi di 300 m. È un particolare esempio in cui le estreme condizioni al contorno hanno indotto a ricorrere ad una soluzione a trave piuttosto che verso schemi strutturali più adatti a queste luci.
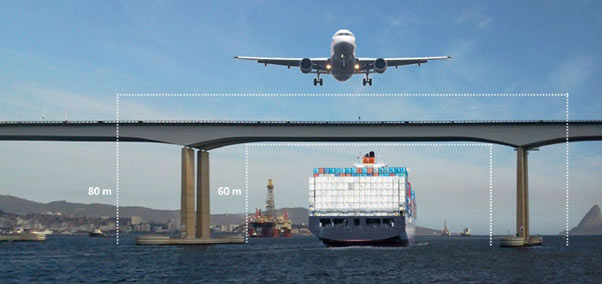
La tipologia della struttura è di tipo a doppio cassone accoppiato a sezione variabile, con altezza massima di 12 m (in appoggio) e minima di 5,6 m (in campata).
Le condizioni estreme erano dettate da una quota sotto trave limite per consentire il transito delle navi Super Panamax (altezza minima di 60 m) e contemporanetamente da una quota sopra trave limite dovuta al percorso di atterraggio per l’Aeroporto Santos Dumont, che ha reso impossibile adottare configurazioni strallate o ad arco.
Per i ponti in carpenteria metallica è possibile individuare principalmente due tipologie, le quali si differenziano dal sistema di impalcato utilizzato:
- Ponti a travata con impalcato a graticcio
- Ponti a travata con impalcato a cassone
Di seguito si riportano valori indicativi dei pesi delle carpenterie metalliche espresse in kg/mq per soluzioni di impalcato a graticcio e a cassone, nel caso di un ponte di larghezza 12,5 m con tracciato rettilineo, al variare della luce delle campate.
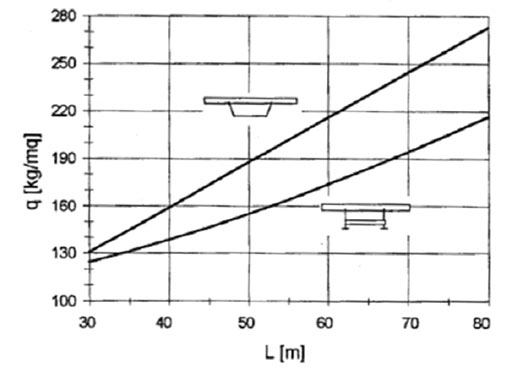
Elementi principali dei ponti a travata
Sia gli impalcati a cassone che a travata semplice sono costituiti dai seguenti elementi principali:
- Travi principali: hanno la principale funzione di gfarantire la capacità portante della struttura. Lo spessore degli elementi varia lungo lo sviliuppo della campata per ottimizzare le quantità di acciaio. I diversi conci sono assemblati in opera tramite bullonatura o saldatura.
Le travi principali vengono solitamente irrigidite tramite fazzoletti metallici a cui collegare i diaframmi trasversali e possono inoltre essere inclinati per consentire di ridurre gli ingombri in corrispondenza degli appoggi e, di conseguenza, delle pile.
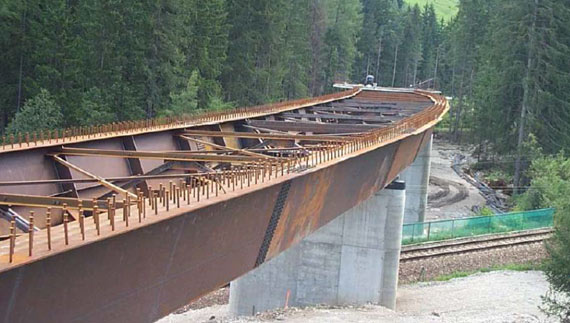
- Diaframmi trasversali: nei ponti a travata collegano le travi del graticcio consentendone un comportamento rigido trasversalmente (applicazione Metodo Courbon), mentre negli impalcati a cassone permettono di garantire il funzionamento a sezione del cassone mantenendo la forma della piana. I diaframmi trasversali possono essere realizzati con differenti conformazioni:
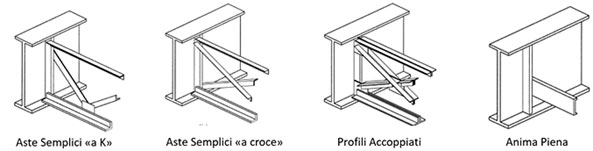
- I traversi a “K”, tipicamente leggeri, vengono impiegati soprattutto per ponti rettilinei.
- I traversi a croce di S. Andrea vengono impiegati nel caso non si vogliano impiegare elementi in compressione, ma solamente a diagonale attiva.
- I traversi accoppiati a “L” o UPN o doppia “L” o UPN vengono impiegati particolarmente nei ponti a cassone o a travata in curva.
- I traversi ad anima piena, che solitamente generano un maggior dispendio di materiale, sono utili ad esempio per sfruttare il comportamento a sezione mista trasversalmente, ma vengono impiegati in alcune soluzioni con impalcati particolarmente larghi, al fine di ridurre la dimensione delle pile, situazioni solitamente convenienti nel bilancio generale dell’opera.Questa soluzione risulta anche molto utile se si decide di realizzare una soletta in lastra ortotropa, avendo la rigidezza maggiore lungo la direzione principale che collabora con tutta la struttura.
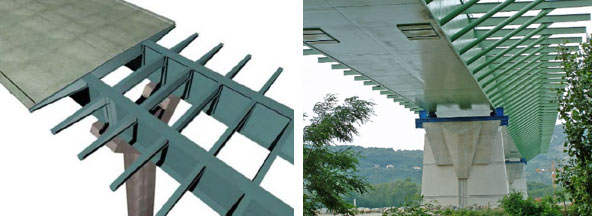
- Elementi di collegamento acciaio-cls per soluzioni miste: permettono la trasmissione delle tensioni di taglio tra acciaio e calcestruzzo consentendone la collaborazione (pioli tipo Nelson, ferri piegati, connettori rigidi, eliche ad asse orizzontale, ecc.).È bene fare in modo che il passo tra una fila di pioli successiva nella direzione dello sviluppo della trave non sia mai maggiore dell’altezza del piolo garantirne un comportamento tipico di puntone-tirante e che quindi il puntone si crei sotto la testa del piolo e che vada a sforzare sulla base del piolo successivo, ottenendo così un sistema di connessione il più rigido possibile.

- Diaframmi superiori: hanno la funzione di bloccare gli effetti di sbandamento della porzione compressa delle travi mantenendo di fatto la sezione chiusa durante le fasi di varo e di getto della soletta, prima che il calcestruzzo faccia presa. In fase di esercizio sono infatti sostituite dall’effetto della soletta.
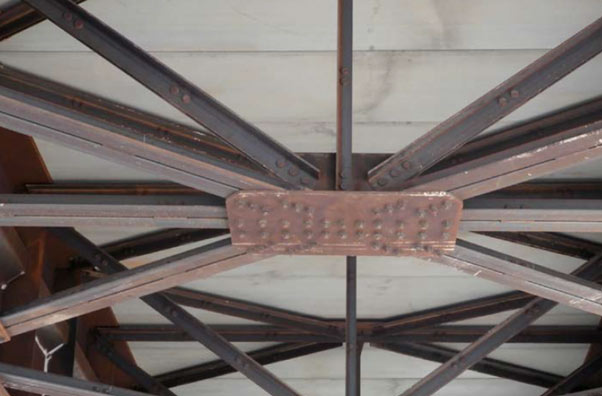
Questi elementi sono fondamentali nella resistenza alle azioni orizzontali esterne della sezione (vento e torsioni dell’impalcato) e per constratare l’effetto di sbandamento delle flange compresse.
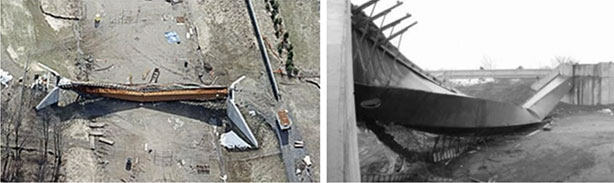
Ponti a travata con impalcato a graticcio
Nai ponti con impalcato a graticcio, l’impalcato è costituito da travi a parete piena, tipicamente costituite da lamiere saldate o, per luci minori, da profili laminati di grande dimensione, ed è dotato di traversi ad “I” o reticolari per la collaborazione fra le stesse travi, disposti con interasse solitamente variabile tra i 5 e gli 8 metri, sulla base delle sollecitazioni torcenti e della configurazione geometrica dell’impalcato.
Normalmente i traversi non solidali alla soletta e vengono saldati o imbullonati agli irrigidimenti verticali delle travi principali.
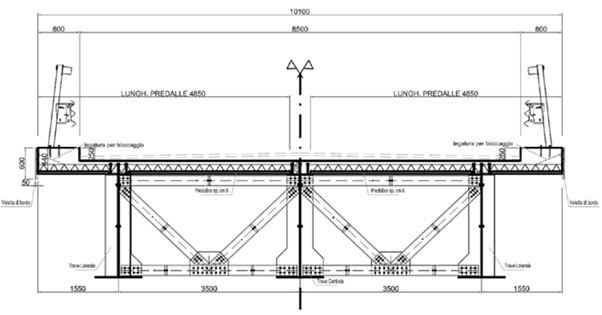
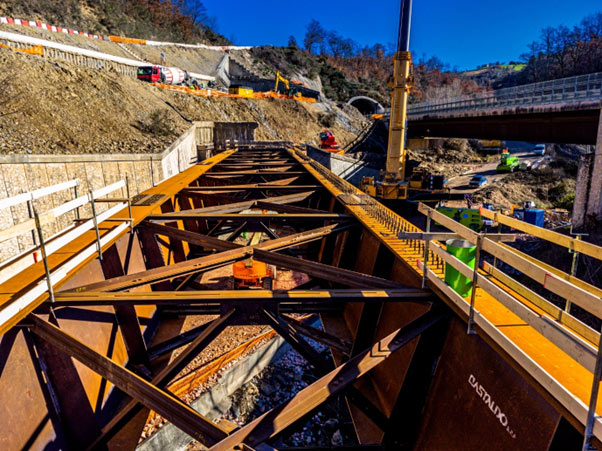
Questo sistema è normalmente utlizzato per coprire campate da 25÷30m fino a 60÷80m.
Esistono differenti configurazioni alternative, fra cui gli impalcati a via di corsa inferiore con travi di tipo reticolare o pieno, utili per attraversamenti di corsi d’acqua con alto valore di piena.
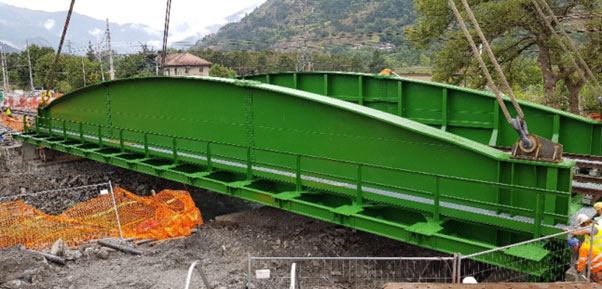
Ponti a travata con sezione chiusa cassone
L’impalcato a cassone è costituito da pareti piene con sezione chiusa in cui la piattabanda inferiore è costituita da un diaframma pieno in acciaio e quella superiore tipicamente da una soletta in cls armato, in modo da sfruttare il comportamento misto fra i due materiali.
I diaframmi intermedi sono generalmente costituiti da reticolari composte da profili commerciali imbullonati agli irrigidimenti delle anime ed alle piattabande, mentre in corrispondenza degli appoggi i diaframmi svolgono anche la funzione di irrigidimenti dei cassoni nei confronti delle azioni verticali concentrate. Spesso i diaframmi di appoggio sono composti da pereti piene in lamiera.
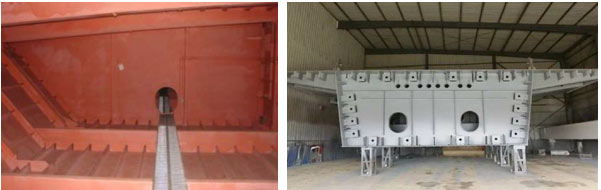
Una trave rompitratta è eventualmente introdotta per fornire appoggio intermedio alla soletta.
La sezione a cassone costituisce un’ottima soluzione strutturale sia quando è richiesta una elevata rigidezza torsionale (impalcati in curva e carichi eccentrici) sia quando si vuole ridurre l’altezza d’impalcato.
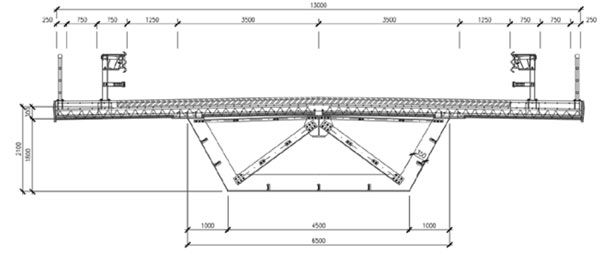
Grazie alla loro eleganza formale, inoltre, i ponti a cassone si inseriscono in modo gradevole nel paesaggio, diventandone un valore aggiunto.
Normalmente queste soluzioni vengono utilizzate per campate fino a 100-150m, in alcuni casi anche oltre.
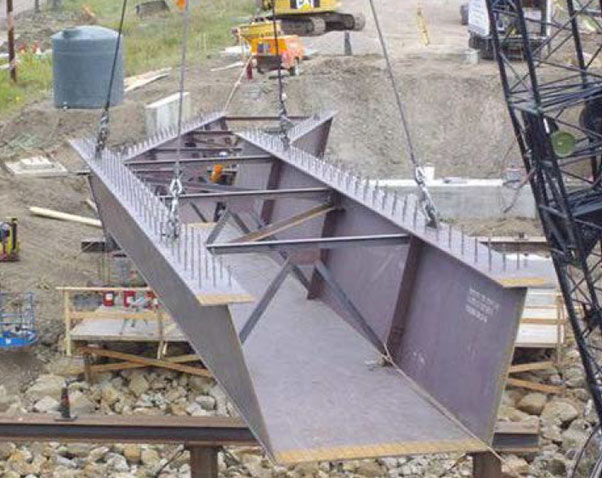
La sezione a cassone è generalmente conveniente se ha una larghezza contenuta (< 5 m).
Il cassone trapezio ha il vantaggio rispetto a quello rettangolare di ridurre la lunghezza degli sbalzi della soletta e di contenere la larghezza inferiore e, conseguentemente, la larghezza delle pile.
L’elevata resistenza a torsione permette di realizzare impalcati di grande larghezza.
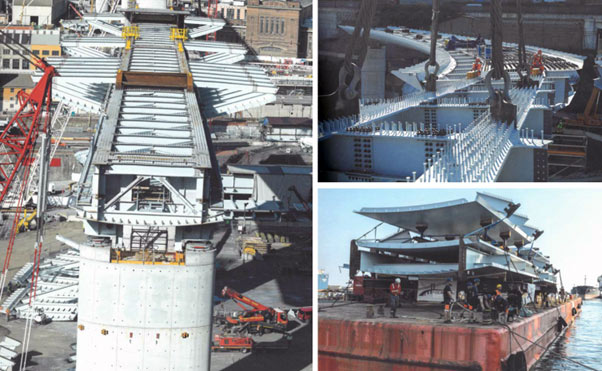
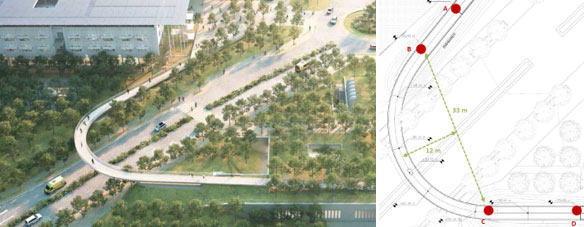
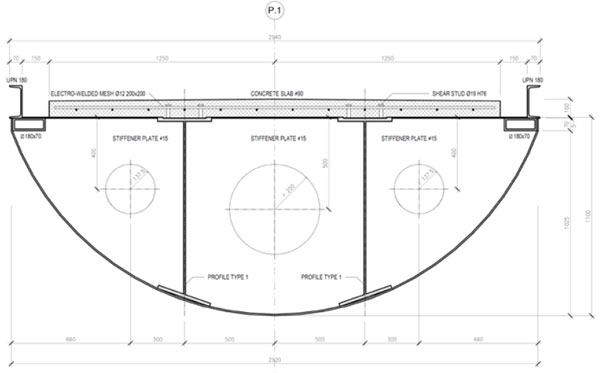
Ponti a travata reticolare
Le soluzioni a travata reticolare sono specialmente impiegate per ponti a via inferiore, in cui si hanno determinati vingoli all’intradosso dell’impalcato dettati da corsi d’acqua con altezza di piena importante.
Questi impalcati, non avendo solitamente limiti di altezza superiore, sono caratterizzati da una elevata rigidezza flessionale e sono di fatto particolarmente indicati per ponti ferroviari, i quali vengono dimensionati con una freccia ammissibile sotto L/1000.
I ponti a travata reticolare sono adatti tipicamente per a campate fino a 200-300 m.
È possibile apporofondire le tipologie di impalcato a partire dal seguente link:
PROGETTAZIONE DEI PONTI A TRAVATA
Di seguito vengono presentate le principali tematiche riguardanti la progettazione dei ponti a travata in carpenteria metallica.
Larghezza impalcato
Il primo tema è sicuramente la definizione della larghezza dell’impalcato. La scelta della soluzione tecnologica da utilizzare dipende dalle caratteristiche geometriche della sezione stradale o dalle condizioni al contorno.
Si riportano di seguito le tipiche sezioni stradali:
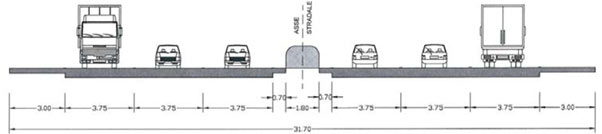
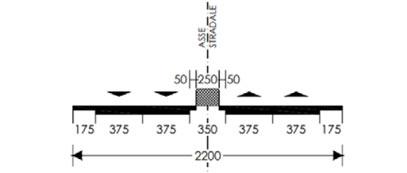
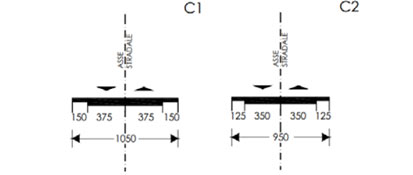
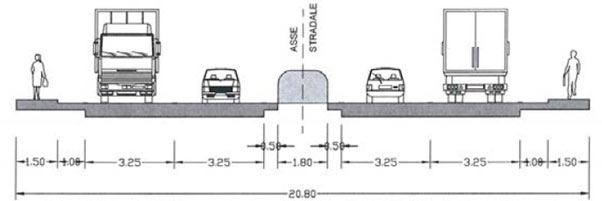
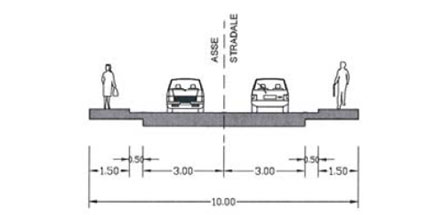
Per queste ultime due categorie la norma richiede l’esecuzione di un marciapiede adeguatamente protetto in ciascuno dei due lati della carreggiata con larghezza minima di 1,5 m.
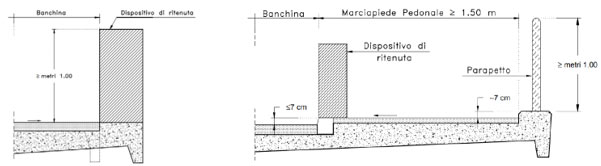
Sono da tenere in conto nel progetto della carreggiata anche gli ingombri dovuti alle barriere di sicurezza, le quali devono consentire la dissipazione di energia per resistere all’impatto di veicoli di diverse categorie. Sia che si tratti di barriere prefabbricate in calcestruzzo sia per le barriere metalliche, il progetto del ponte deve garantire lo spazio per la deformazione della barriera.
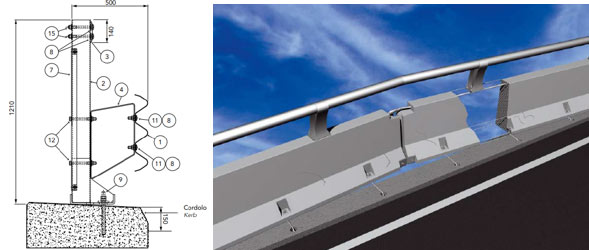
È infine necessario considerare l’eventuale presenza di barriere antirumore, sia in termini di ingombri sia di peso.
Limiti quota intradosso impalcato
Nel caso di cavalcavia o sovrappassi, è da rispettare l’altezza libera di 5 m da piano carrabile per consentire il transito inferiore dei veicoli ed evitare impatto con i veicoli stessi sottostanti.

Nel caso di corsi d’acqua è inoltre da rispettare l’altezza nelle condizioni di massima piena (con Tr = 200 anni) garantendo anche un’ulteriore franco di 1,5 m per l’eventuale transito di materiale solido (es. transito di tronchi d’albero) e tenendo in considerazione potenziali effetti di rigurgito e quindi l’aumento del tirante d’acqua a monte dell’ostacolo rappresentato dalle eventuali pile in alveo.
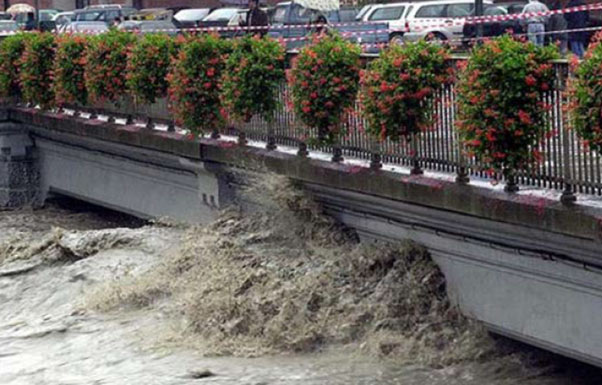
A tal proposito, gli impalcati a via di corsa inferiore con travi di tipo reticolare o pieno, utili per attraversamenti di corsi d’acqua con alto valore di piena, consentono di ridurre l’ingombro dell’impalcato all’intradosso.
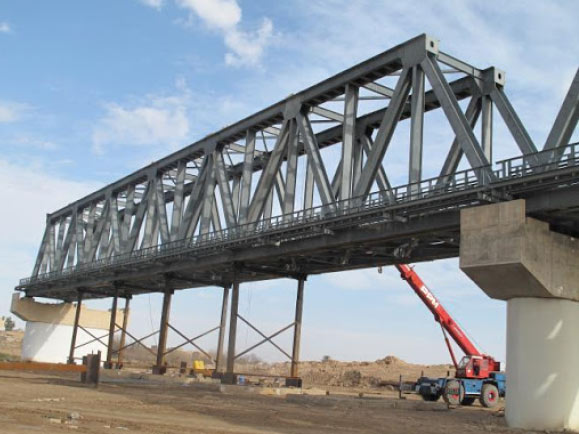
Geometria tracciato
Per tracciati curvilinei è opportuno tenere presente la possibile variabilità della larghezza di impalcato in pianta. Sono tipicamente previsti aumenti di larghezza della banchina per garantire la visibilità agli utenti della strada e delle corsie per consentire ai veicoli di poter curvare senza fuoriuscire dalla corsia stessa.
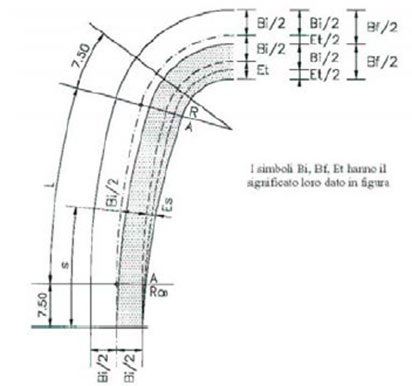
Da questi aspetti possono nascere le seguenti difficoltà legate dunque ad una differente dimensione degli sbalzi della soletta e del passo fra le travi e ad una differente lunghezza e sollecitazione delle travi longitudinali di impalcato.
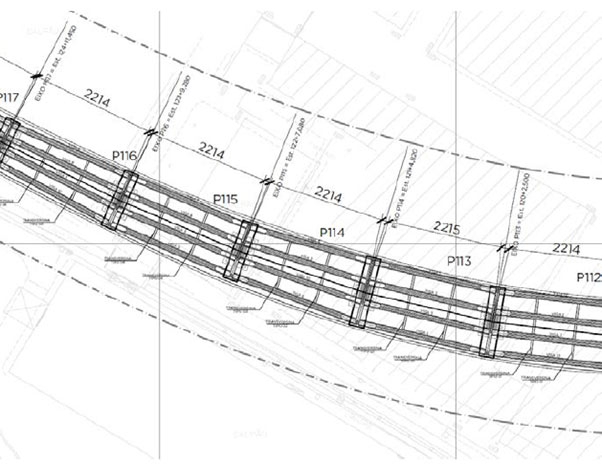
Nella progettazione delle strutture in acciaio a travata con tracciato in curva è necessario considerare inoltre che, oltre all’eccentricità dei carichi verticali, le travi dell’impalcato avranno rigidezze flessionali differenti.
Per far fronte a queste problematiche solitamente si agisce facendo variare l’interasse delle travi e gli spessori dei piatti che compongono le travi principali.
Soluzione per la soletta
Nella scelta della tipologia di soletta verranno prese in considerazione sicuramente quelle soluzioni che permettono di risparmiare sui pesi complessivi dell’impalcato, la velocità di esecuzione, la possibilità di sollevamento dal basso.
Di seguito si riportano le soluzioni per le solette di impalcato più diffuse:
Lastre predalle: spessore 5-7 cm in cls prefabbricato con getto in opera (più diffusa) che permette di comprire sia le campate centrali sia quelle laterali nella direzione trasversale. Offre il vantaggio di una facile posa e del sistema resistente a struttura mista. Ha lo svantaggio di dover aspettare la maturazione del calcestruzzo per poter continuare con la messa in opera della struttura.
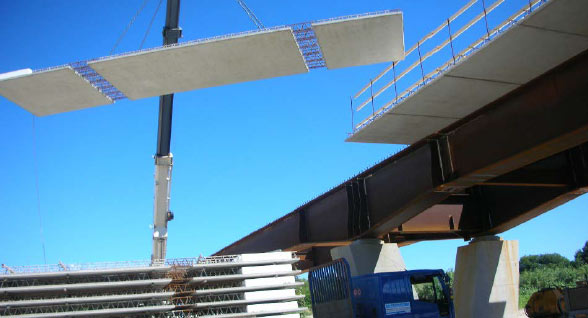
Lastre prefabbricate in c.a.: eventualmente pretese, portano il vantaggio di non dover attendere il getto di completamento e presentano delle tasche nelle quali vengono concentrati i connettori che vengono riempiti con malte cementizie con velocità di maturazione e sviluppo resistenza più performanti.
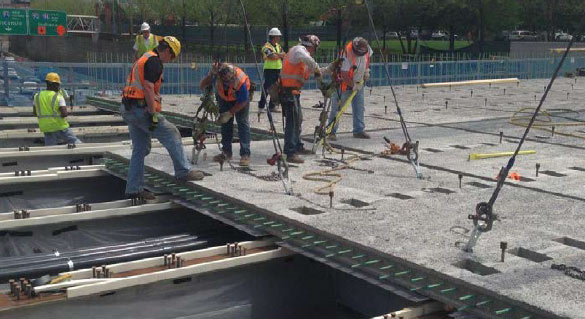
Lastre ortotrope in acciaio: al prezzo di un maggiore dispendio di acciaio (nell’ordine di +100 kg/mq), offrono il grande vantaggio conferire la massima leggerezza essendo la struttura costituita interamente in acciaio. La lastra ortotropa è costituita da una piastra in acciaio irrigidita inferiormente con profili tipicamente a cassoncino o a T e consente l’ulteriore vantaggio di avere piattabanda continua superiore nelle zone di momento negativo. I costi generali aumentano ma maggiore leggerezza e velocità rispetto alle soluzioni miste e permettono di ottimizzare gli spessori di asfalto solitamente inferiori.
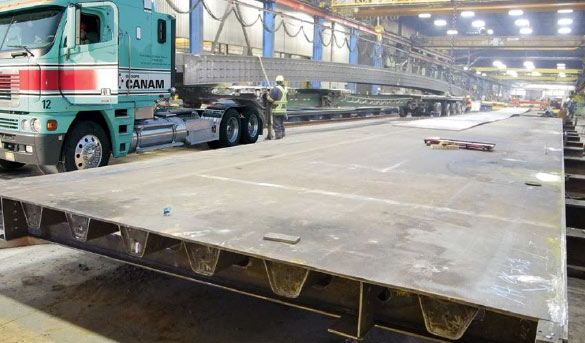
È possibile approfondire l’argomento sulle tipologie di solette per i ponti al seguente link:
Pavimentazione e finitura
Per le strutture miste si dispone un primo strato di binder (40-60 mm) al di sotto dello strato di usura (30-40mm). Negli impalcati con lastra ortotropa, il conglomerato può essere ridotto ad un unico strato a patto che venga garantita la resistenza meccanica e l’adesione al supporto (sp. 40 mm).
Lo strato di binder viene solitamente realizzato di spessore superiore, nonostante la sua rigidezza, per andare a regolarizzare le irregolarità del getto della soletta in calcestruzzo permettendo di ricreare la forma prevista da progetto stradale.
La precisione del supporto della soletta ortotropa permette di impiegare un singolo strato di usura di tipo misto di circa 4 cm, riducendo ulteriormente i carichi e quindi il peso strutturale.
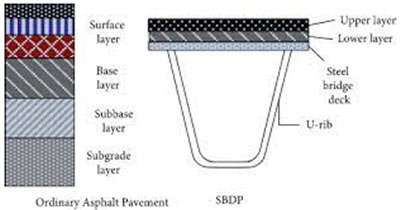
Materiali utilizzati
Per la scelta della tipologia di acciaio da utilizzare si terrà in conto sia della classe di resistenza “S” dell’acciaio sia dei valori minimi di resilienza sulla base delle temperature di progetto, degli spessori dei piatti, della percentuale di sforzo a cui sarà sottoposto ciascun elemento.
È possibile approfondire l’argomento sugli acciai per i ponti dal seguente link:
A partire dal seguente link è inoltre possibile scaricare un tool di calcolo per la selezione dell’acciaio in funzione della tenacità e delle proprietà attraverso lo spessore di elementi saldati per i quali esiste un rischio significativo di strappo lamellare durante la produzione, in accordo all’Eurocodice 3 parte 1-10 (cliccare sul + per aprire i download delle schede):
Il calcestruzzo costituente la soletta verrà selezionato in base alla classe di esposizione e alla durabilità, in accordo a quanto prescritto dalle NTC 2018.
Protezione contro la corrosione
La scelta delle soluzioni per la protezione delle strutture metalliche dipende dalle caratteristiche del progetto e dalle condizioni ambientali.
Dopo la definizione della vita nominale della struttura, sarà necessario prevedere l’individuazione della classe di corrosività dell’ambiente nella zona in cui il ponte verrà realizzato (secondo la norma UNI EN ISO 9223-2012) e la conseguente identificazione della durabilità dei sistemi di protezione alla corrosione a seconda del tipo di protezione scelta.
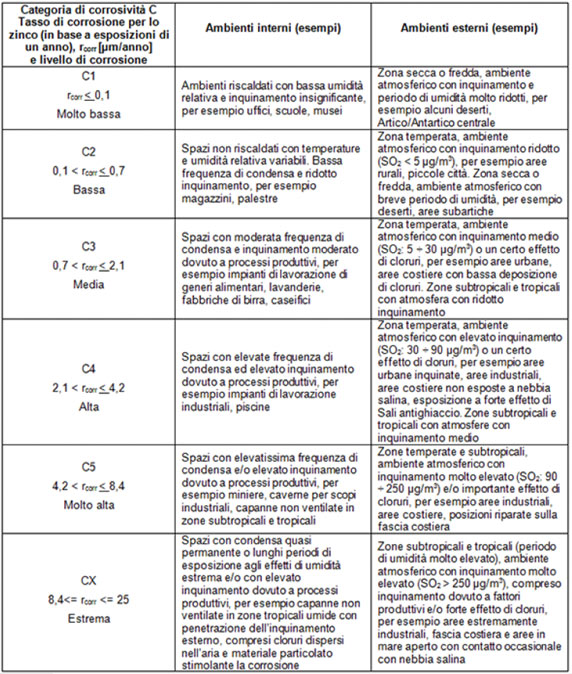
Le soluzioni maggiormente utilizzate per i ponti sono le seguenti:
- Zincatura a caldo: offre l’enorme vantaggio di garantire un’ottima protezione dalla corrosione e dunque di ridurre al minimo la manutenzione dei manufatti Comporta tuttavia alcune difficoltà nel caso di saldature eseguite in opera e la conseguente necessità di metallizzare il materiale con strato più spesso in seguito alle operazioni di saldatura (molto adatti a ponti realizzati mediante conci imbullonati). Sono inoltre da tenere in conto alcune limitazioni in termini di peso e sulle dimensioni dei manufatti zincabili in stabilimento.
- Verniciatura: permette la protezione del materiale base tramite l’applicazione in cantiere a seguito della saldatura. Più economica inizialmente, ma necessita di diversi cicli durante il trattamento e deve essere ripristinata continuamente durante la vita del ponte.
- Acciaio auto passivante (ex CorTen): adatto ad ambienti che non presentano elevato grado di umidità o presenza di cloruri, che possono instabilizzare la patina di ossido e accelerare il processo di corrosione. Molto spesso o in ambienti marini, in presenza di cloruri, di attacchi chimici, di dilavamento di acque o o ancora di umidità elevata (ad esempio per porzioni all’interno dei ponti a cassone) è possibile che l’acciaio non sia in grado di sviluppare il film di ossido in maniera stabile o viene dilavato continuamente e si possono pertanto verificare fenomeni di delaminazione o di pitting (corrosione localizzata) col rischio di non garantire la durabilità tipica delle strutture se opportunamente utilizzate.
Nel caso dei ponti a cassone può essere utile verniciare l’interno del cassone, rinunciando però all’effetto della passivazione nella parte interna e facendo comportare il materiale come un tipico acciaio al carbonio protetto con verniciatura. Un ulteriore accorgimento può essere la disposizione di aperture per garantire una maggiore ventilazione.
Per elementi in acciaio autopassivante è opportuno inoltre utilizzare bulloneria appropriata nel medesimo materiale o connettori imbruniti (neri) che hanno al loro interno degli elementi chimici (nichel, cromo, molibdeno) che di fatto conferiscono caratteristiche di resistenza simili a quelle dell’acciaio autopassivante, evitando la creazione di punti deboli.
È possibile approfondire l’argomento sulle soluzioni per la protezione contro la corrosione per i ponti in acciaio a partire dal seguente link:
Carichi
In generale, nella progettazione dei ponti vengono considerati i seguenti carichi:
- Carichi permanenti:
- Carichi permanenti di prima fase (montaggio): carpenterie metalliche e soletta (G1);
- Carichi permanenti di seconda fase (esercizio): cordoli, pavimentazione, velette, barriere e parapetti (G2);
- Carichi variabili da traffico attraverso differenti schemi di carico da utilizzare per le verifiche globali e locali; la disposizione dei carichi ed il numero delle corsie sulla superficie carrabile saranno volta per volta quelli che determinano le condizioni più sfavorevoli di sollecitazione per la struttura, membratura o sezione considerata;
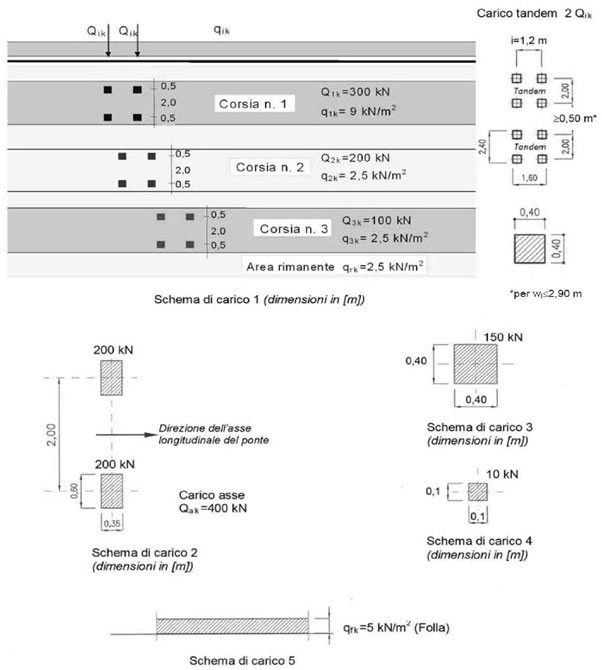
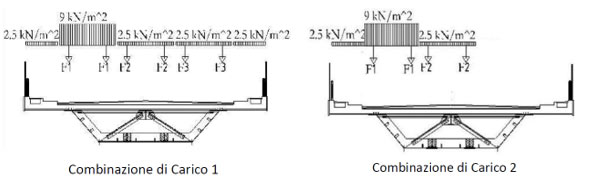
I carichi da traffico verranno combinati attraverso lo studio delle linee di influenza, che consentono di calcolare le sollecitazioni e gli spostamenti di ciascuna sezione resistente al variare della posizione dei carichi sia lungo l’asse del ponte (linea di influenza longitudinale), sia lungo la larghezza dell’impalcato (linea di influenza trasversale)
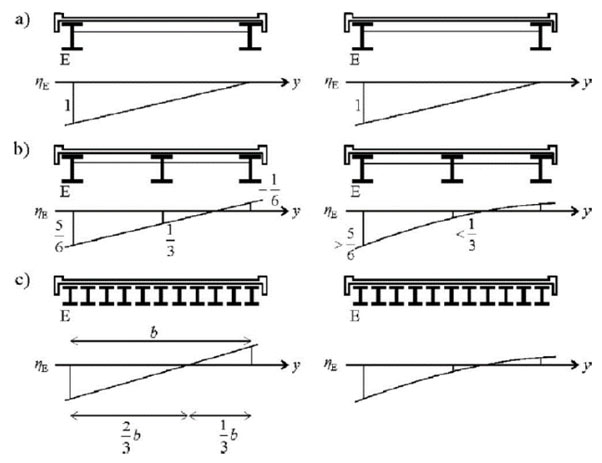
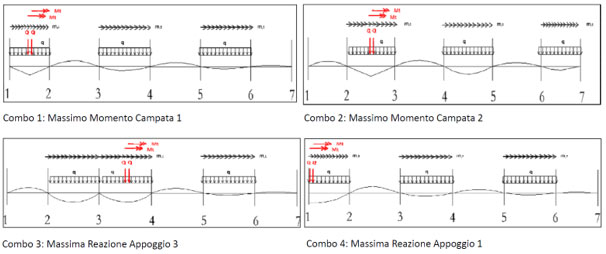
- Azione longitudinale di frenamento e accelerazione (lungo l’asse dell’impalcato);
- Azione centrifuga (ortogonale all’asse dell’impalcato), legata alla sommatoria dei carichi tandem ed al raggio di curvatura del tracciato planimetrico. Nel caso di raggi di curvatura maggiori di 1500 m la forza centrifuga si può trascurare;
- Resistenze parassite sui vincoli: azioni legate alla tipologia di vincolo, all’entità del carico verticale applicato (utilizzate per il dimensionamento dei vincoli e dei loro sistemi di ancoraggio);
- Azione del vento, con opportuni coefficienti di forma (EC1-4 par. 8), considerata come forza statica equivalente. Sono da tenere in conto gli effetti dinamici dovuti al vento (effetto del distacco dei vortici), che possono creare effetti di carico alternati verticali alla struttura del ponte;
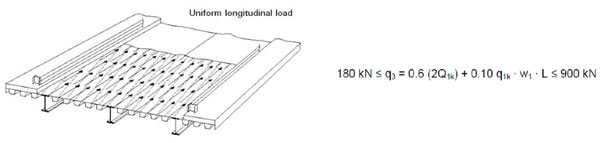
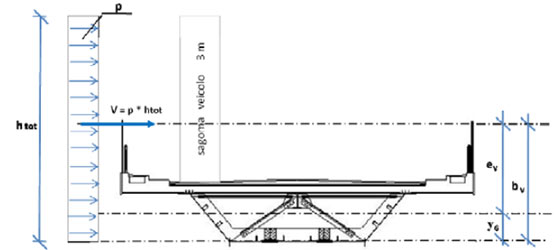
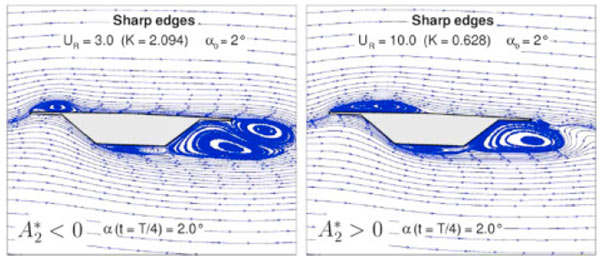
- Azioni sismiche: nel caso degli impalcati da ponte, che devono rimanere in campo elastico, gli effetti sismici sono poco importanti. Particolare attenzione sarà da tenere per gli elementi verticali (pile);
- Deformazioni imposte:
- Deformazioni viscose delle solette in calcestruzzo, considerata attraverso un modulo elastico ridotto per considerare gli effetti di deformazione a carico costante del calcestruzzo;
- Ritiro del calcestruzzo delle solette considerato come una coazione all’interno della struttura mista;
- Coazioni derivanti da cedimenti differenziali delle pile. In mancanza di studi geotecnici che dimostrino gli effettivi valori dei possibili cedimenti differenziali, è buona pratica verificare le strutture dell’impalcato per un cedimento massimo di 50 mm. Nel caso di ponti in carpenteria metallica questa problematica è relativamente contenuta;
- Deformazioni termiche dell’impalcato di tipo costante lungo la sezione o con gradiente di temperatura tra soletta e impalcato metallico. La variazione costante (tipicamente 25°) è solitamente usata per dimensionare i giunti di dilatazione, la variazione differenziale porta tipicamente ad effetti di flessione nell’impalcato;
Predimensionamento e suddivisione in conci
L’altezza della sezione del ponte viene scelta in funzione della dimensione delle campate e della larghezza di impalcato, per consentire l’ispezione della struttura e per garantire il corretto comportamento trasversale.
Per ponti a travata con impalcato a graticcio è possibile fare riferimento ai seguenti rapporti luce/altezza della sezione della sola parte metallica:
- Impalcato bi-trave in semplice appoggio ad altezza costante: L/h = 22÷25 m
- Impalcato bi-trave continuo ad altezza costante: L/h = 28 m
- Impalcato bi-trave continuo ad altezza variabile: L/h = 25 sulla pila, 50÷60 m sulla spalla, 40÷50 m in mezzeria
Per ponti a travata con impalcato a cassone continuo:
- h/l = 1/36 (B/12) ^0,7, con B pari alla larghezza dell’impalcato in metri
- In alternativa: L/h = 35 m
Il calcolo delle sollecitazioni sulle strutture metalliche può essere eseguito attraverso metodi classici che permettono di determinare la linea di influenza trasversale e quindi come un carico mobile effetto sulle varie travi al variare della sua posizione:
- Engesser – Courbon (ipotesi traversi rigidi a flessione): si ipotizza che la sezione ruoti o trasli rigidamente attorno al proprio asse. Utile per il predimensionamento di ponti con traversi a passo ridotto;
- Massonet: impalcato deformabile trasversalmente, confronta il comportamento della rigidezza flessionale delle travi longitudinae con l’effettiva rigidezza dei traversi. Metodo complesso e meno impiegato
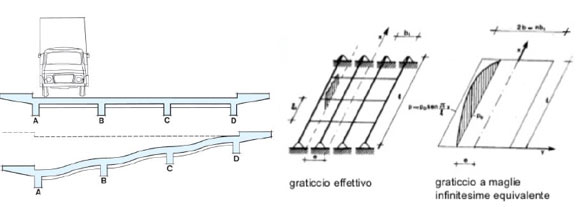
Oppure attraverso metodi numerici con software di calcolo agli elementi finiti.
La suddivisione in conci dell’impalcato continuo è fatta secondo i seguenti criteri:
- Prima suddivisione effettuata secondo la distribuzione del momento dovuto ad un carico uniformemente distribuito;
- I conci di maggior dimensione (15 m) vengono disposti a cavallo degli appoggi (zone di momento massimo per impalcati continui) e, in secondo luogo, in campata per evitare di aver connessioni eccessivamente sollecitate;
- Per ciascun concio è scelto lo spessore delle piastre ottimizzato. I maggiori spessori si trovano sui conci in appoggio;
- Le prime ipotesi di suddivisione in conci devono poi essere confermate fa un modello agli elementi finiti preliminare.
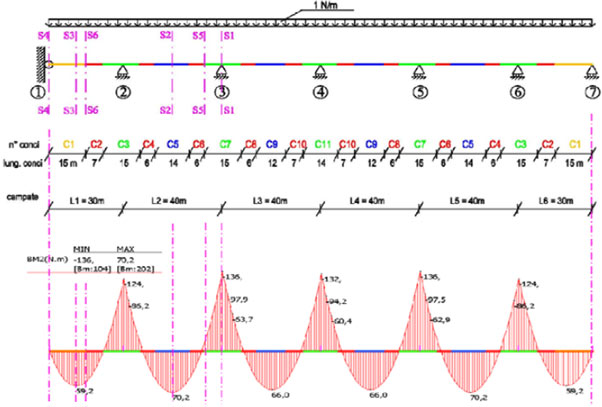
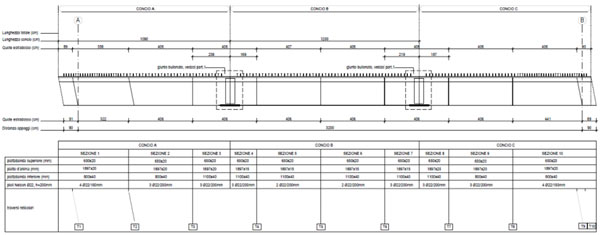
Definizione caratteristiche meccaniche delle sezioni
Le caratteristiche della sezione mista acciaio-calcestruzzo sono calcolate per ogni concio considerando l’interazione fra i due materiali.
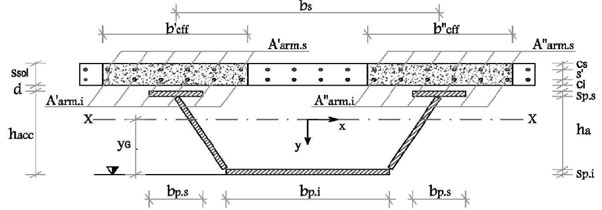
Nei pressi degli appoggi, dove la soletta è in trazione, non è considerato il contributo della soletta (ma solo dell’armatura tesa). Le sezioni di appoggio sono normalmente quelle dimensionanti.
È necessario effettuare il calcolo delle caratteristiche di ogni concio in ciascuna delle seguenti condizioni:
- Sezione di solo acciaio (fasi di montaggio): soletta considerata come carico sulle strutture metalliche
- Sezione mista a tempo iniziale omogeneizzata all’acciaio – coefficiente di omogeneizzazione n0 = Ec,0/Es
- Sezione mista a tempo infinito omogeneizzata all’acciaio – ninf = Ec,inf / Es
A tempo infinito è necessario considerare gli effetti di viscosità che portano alla riduzione del modulo elastico del calcestruzzo della soletta. In campata dunque i carichi andranno a ripartirsi diversamente.
Predimensionamento delle sezioni in acciaio
Tramite un software agli elementi finiti si creano solitamente 3 modelli di trave continua su 7 appoggi applicando alle sezioni le rigidezze calcolate in precedenza per ciascuna delle condizioni studiate (montaggio, esercizio e tempo infinito).
Vengono eseguiti dei predimensionamenti delle sezioni considerando le massime tensioni applicate all’acciaio allo SLU. Vengono considerate le tensioni di flessione (Navier), taglio (Jourawski) e torsione (Bredt).
Lo spessore d’anima e delle piattabande in ciascuno dei conci è scelta in maniera tale da ottenere valori di tensione compatibili con la resistenza ultima dell’acciaio S355, secondo il criterio di Von Mises.
Allo stesso modo è predimensionata l’area di armatura longitudinale da posizionare nelle solette.
Classificazione delle sezioni resistenti.
Le membrature devono essere inquadrate secondo la classificazione delle NTC 2018 per evidenziare il rischio di effetti di instabilità locale, tipici delle sezioni snelle in classe 4.
I metodi per tenere in conto l’effetto dell’instabilità locale si dividono in due tipologie proposti dalla UNI EN 1993-1-5:
- Metodo della larghezza efficate: vantaggio perché permette di ripartire le tensioni a piatti più tozzi;
- Metodo delle tensioni ridotte: utili per sezioni non standard.
In aggiunta, l’effetto di trascinamento del taglio (shear-lag) tiene in conto della deformazione tagliante delle piattabande sollecitate a compressione o trazione, considerandone una larghezza efficace ridotta. Questo effetto tiene in conto della non uniforme distribuzione delle tensioni in un piatto.
Questi fenomeni si traducono nella riduzione dell’area efficace dei piatti di acciaio (nel caso dello shear lag agente sia sui piati in trazione che in quelli in compressione).
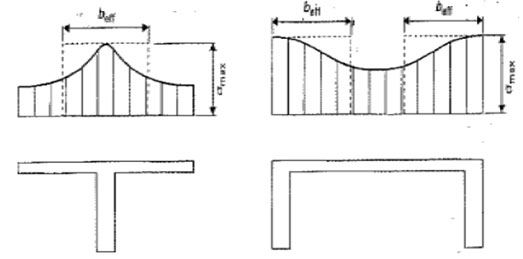
Il calcolo della larghezza efficace tramite il metodo della larghezza efficace si traduce in un problema iterativo: la perdita di area dipende dallo stato tensionale, ma genera a sua volta la variazione dello stato tensionale nella sezione.
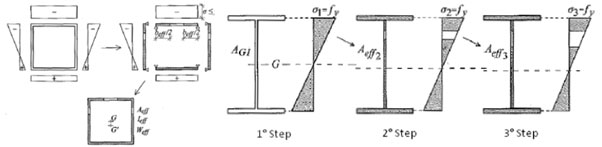
Nel caso delle sezioni ad I o chiuse (cassoni), l’EC3-1-5 permette una procedura semplificata in due passaggi successivi per il calcolo delle caratteristiche efficaci delle sezioni in classe 4:
- Calcolo delle aree efficaci delle piattabande compresse considerando l’area lorda di anime e delle piattabande tese;
- Calcolo dell’area efficace delle piattabande calcolate a partire dalla sezione con area efficace delle piattabande compresse.
Nel caso delle piastre compresse, l’EC3-1-5 determina gli effetti di instabilità confrontando l’instabilità di colonna con gli effetti di instabilità di piastra per ottenere il valore dell’area efficace che sarà interpolazione dei due coefficienti riduttivi.
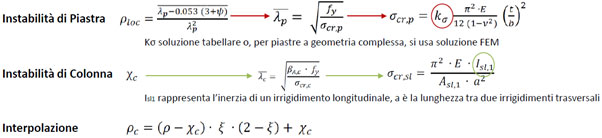
L’area efficace di un pannello irrigidito è data dal confronto di tutti i meccanismi di instabilità che si possono verificare.
Le anime delle travi e dei cassoni devono essere verificate contro gli effetti di instabilità locale delle anime piane dovuta ai carichi verticali concentrati. Le verifiche devono essere condotte secondo la trattazione dell’Eurocodice 3 parte 1-5.
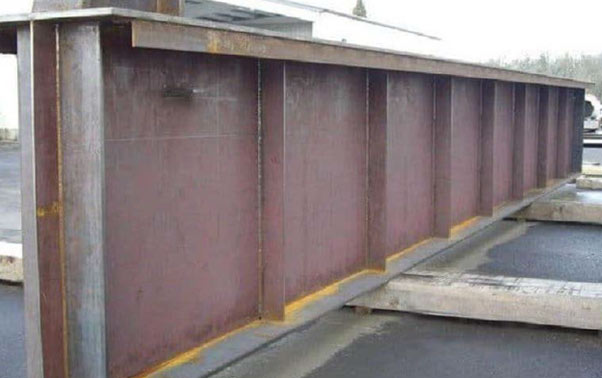
Gli irrigidimenti sono posizionati sia in direzione longitudinale che in direzione trasversale per migliorare il comportamento a piastra dei sottopannelli. Di seguito alcuni esempi delle tipologie di irrigidimenti più utilizzati:
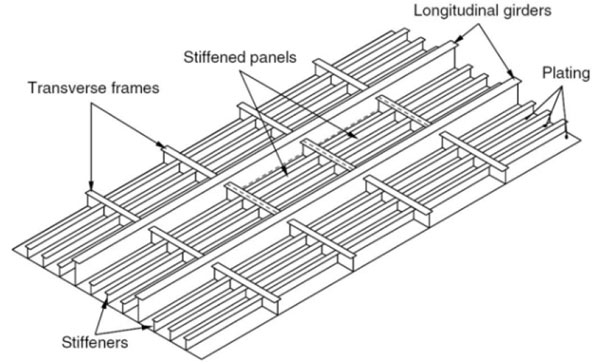
Una volta definite le caratteristiche geometriche e meccaniche delle sezioni di verifica è possibile procedere alle verifiche finali di resistenza allo SLU.
A seguito del predimensionamento e della definizione degli irrigidimenti si crea un modello agli elementi finiti per le verifiche definitive e per il calcolo del comportamento sismico.
Particolare attenzione va posta nella modellazione dell’interazione soletta – cassone per riuscire ad ottenere le sollecitazioni totali agenti sulla sezione.
Inoltre, ricordandosi del fatto che in corrispondenza degli appoggi si ha momento negativo, di fatto la soletta si fessura ed è importante che nel modello di calcolo di consideri questo aspetto.
I diaframmi intermedi vengono dimensionati per assorbire la variazione di momento torcente provocata dai carichi applicati tra un diaframma ed il successivo. Il diaframma reticolare si oppone alla perdita di forma della sezione reagendo con lo schema di forze riportato di seguito:
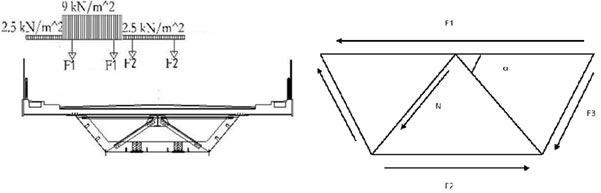
La verifica delle aste del diaframma è effettuata attraverso modelli numerici, considerando la condizione di carico che genera la massima torsione.
Per ponti con tracciato in curva la torsione è generata anche dai pesi propri e dai carichi permanenti simmetrici, le sollecitazioni sui traversi sono di maggiore entità.
Le forze sulle varie aste su di un elemento trasversale a graticcio vengono stabilite prendendo la torsione massima generata nella lunghezza di influenza, nel passo tra un traverso e l’altro, e applicando questa torsione alle aste del traliccio.
Ci saranno elementi compressi e tesi che vanno a resistere alla massima torsione generata nell’impalcato, applicando i carichi tandem in corrispondenza del traverso.
L’eventuale trave rompitratta è predimensionata come una trave continua su più appoggi soggetta alle reazioni trasmesse dalla soletta. La verifica è condotta tramite modello agli elementi finiti. Le azioni scaricate dalla trave devono essere considerate nel calcolo dei traversi intermedi e di appoggio.
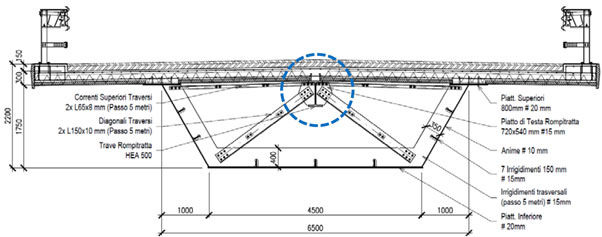
I controventi nella porzione superiore dell’impalcato sono dimensionati per sostenere la spinta del vento sull’impalcato in fase di varo e di getto delle solette trasmettendoli ai diaframmi di appoggio. In fase di esercizio la funzione dei controventi superiori è sostituita dalla molto più rigida soletta in cemento armato.
Il calcolo delle sollecitazioni sui pioli si esegue con la formula di Jourawski confrontandola con i meccanismi di rottura le cui le formule di resistenza riportate nelle NTC.
Le sollecitazioni di taglio applicate ai pioli non comprendono i pesi propri di acciaio e soletta che sono applicati alle sezioni di solo acciaio.
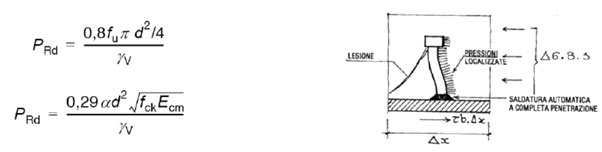
Collegamenti
Le varie componenti della struttura vengono composte a piè d’opera tramite saldature e bullonature.
Le connessioni bullonate vengono generalmente impiegate per i seguenti due usi:
- Connessione di elementi principali (anime e piattabande), in alterativa alla saldatura;
- Connessione di elementi secondari (traversi, controventi e sbalzi). Di norma è il sistema più utilizzato.
Per i collegamenti bullonati sarebbe opportuno far lavorare le unioni ad attrito allo SLE per evitare eccessive deformazioni.
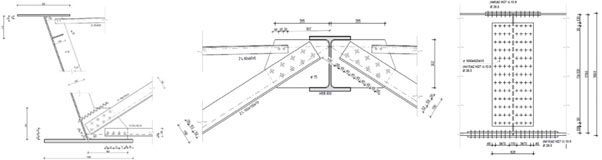
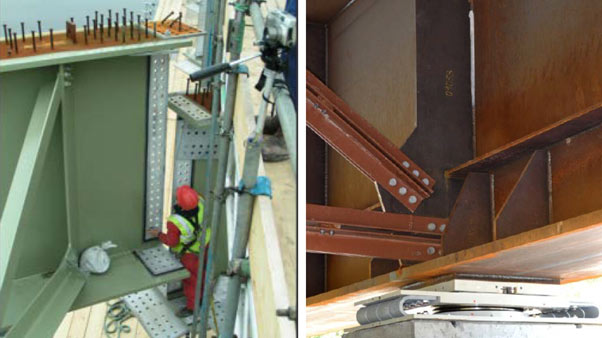
Per quanto concerne i collegamenti saldati, la saldatura viene eseguita in officina tipicamente per saldare i piatti a formare le sezioni d doppio T.
Le saldature in opera vengono impiegate per la connessione dei conci a completa penetrazione.
Il vantaggio di saldare i conci permette di adattare lo spessore dei piatti di acciaio lungo i vari conci e permette di ridurre il peso totale dell’impalcato.
Nel progetto sarà opportuno evitare di prevedere le saldature in corrispondenza delle sezioni più sollecitate e sarà necessario interrompere lo strato di protezione in corrispondenza delle saldature e di proteggere successivamente l’area tramite verniciatura o metallizzazione con spray zincante. Anche gli irrigidimenti devono essere interrotti prima della sezione di giunzione.
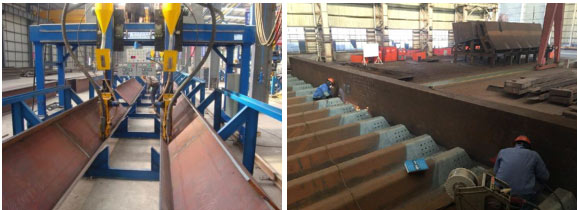
È possibile approfondire l’argomento sui collegamenti a partire dal seguente link:
Verifiche a fatica
Il fenomeno della fatica può essere considerato come la tendenza di una struttura sottoposta ai carichi ciclici lungo la propria vita a creare degli effetti di allineamento delle potenziali zone fragili (cricche), tipiche per strutture leggere come quelle in acciaio.
Per i dettagli sensibili a fatica è necessario condurre opportune verifiche basate sulla tipologia di dettaglio e sullo sbalzo di tensioni a cui il dettaglio è sottoposto:
- Verifiche per la vita illimitata: con riferimento ad un tipico dettaglio attraverso una verifica tensionale;
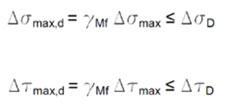
- Verifiche di danneggiamento: obbligatoria per alcuni tipi di dettaglio (pioli nelson e barre d’armatura). Il limite di danneggiamento cumulativo (sommatoria del n. di cicli avvenuti ad un certo valore di tensione) deve essere minore dell’unità.
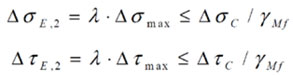
È possibile ricondursi a metodi semplificati che adottano opportuni coefficienti che tengono in conto di diversi aspetti fra cui la lunghezza della superficie di influenza del dettaglio, il volume di traffico e la vita di progetto del ponte.
Le verifiche vengono ripetute per tutti i dettagli potenzialmente soggetti a fatica (giunti bullonati tra conci, saldature degli irrigidimenti longitudinali, dei pioli e saldature di piattabande e anime) alternando i due metodi.
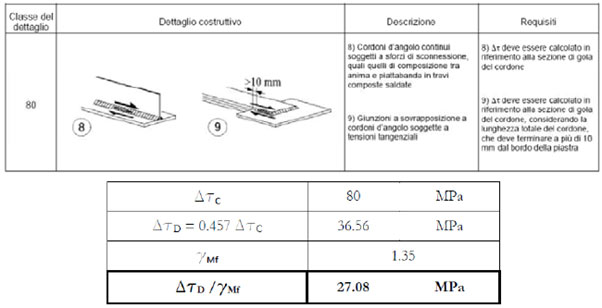
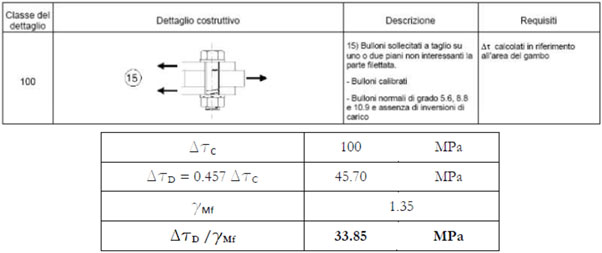
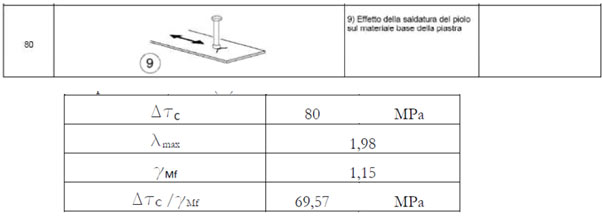
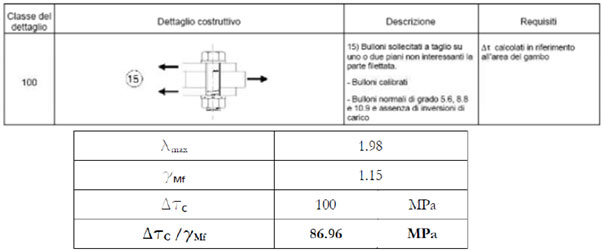
Verifiche di deformabilità dell’impalcato
La norma non definisce un valore limite alla deformabilità ma affermano che deve risultare compatibile con la geometria della struttura stessa in relazione alle esigenze di progetto e che non deve arrecare disturbo al transito dei carichi mobili alle velocità di progetto della strada.
In genere si assume, per gli abbassamenti legati ai carichi accidentali in combinazione frequente il limite Flim = L/500
Le deformazioni dell’impalcato date dai carichi permanenti sono solitamente equilibrate con la contromonta iniziale data all’impalcato metallico.
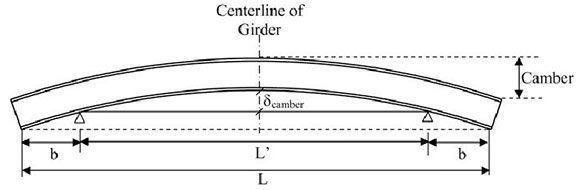

Le contromonte possono essere applicate con sistemi a freddo (più comune con martinetti idraulici) o a caldo direttamente in officina scaldando la parte superiore della trave.
La deformabilità della struttura da ponte deve tenere conto della storia di carico della struttura considerando le differenti condizioni di vincolo (condizioni finali o provvisorie di varo) e le differenti rigidezze (condizioni con soletta collaborante e non collaborante).
Controllo incidenze delle carpenterie metalliche
Al termine delle verifiche si esegue solitamente un controllo delle incidenze dell’acciaio, confrontandole con i comuni valori di predimensionamento.
Di seguito si riporta, a titolo di esempio, il peso delle carpenterie metalliche per un ponte a 7 campate centrali di luce 40 m e campate laterali da 30 m con impalcato a cassone di larghezza 13 m.
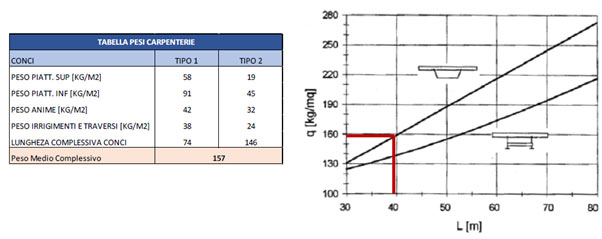
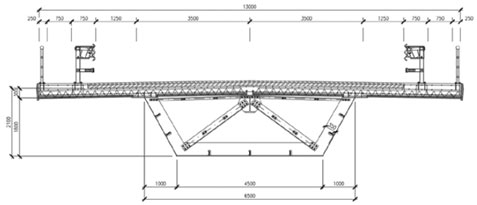